Taking the oil refining industry as an example, at present, domestic and foreign high-temperature hot oil pumps generally use contact bellows single end mechanical seals. The average service life of domestic bellows mechanical seals is about one year, and that of imported bellows mechanical seals can be more than two years. However, various flushing and cooling measures must be taken on the base wood (Figure 9-1) to reduce friction temperature rise and prevent coking, heat cracking Seal failure is caused by bellows loss of elasticity, bellows fracture, pump evacuation, aging of seals, etc. For this reason, a large amount of flushing oil and cooling water must be consumed, resulting in high operating costs (preliminary estimates indicate that the annual operating costs for flushing and cooling of a hot oil pump exceed 100000 yuan), large energy consumption, poor sealing reliability, low safety and high maintenance costs.
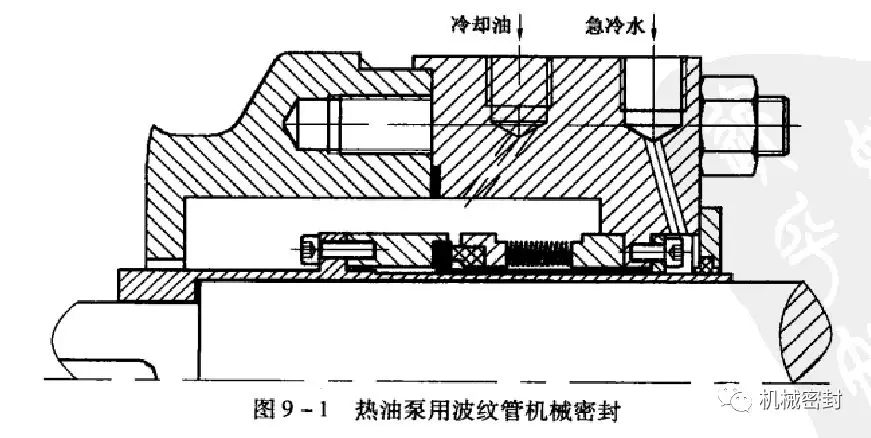
Scheme 21 (Fig. 9-2) and Scheme 32 (Fig. 9-3) are two auxiliary measures for flushing and cooling of bellows mechanical seal for high-temperature hot oil pump in API 682 standard.
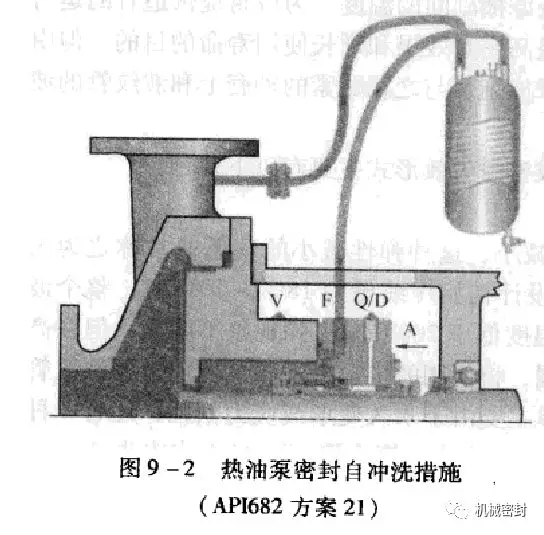
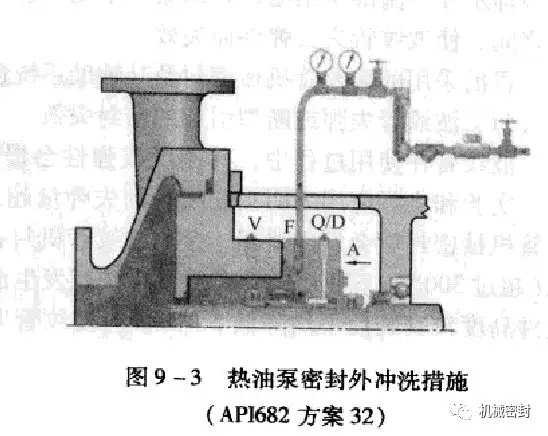
Scheme 21 is self flushing plus quenching at the back of stationary ring. Self flushing means that the high-temperature hot oil pressurized at the pump outlet is led to the sealing chamber after cooling and cooling, and the sealing elements are cooled directly; At the same time, cooling water is usually injected into the back of the stationary ring to quench it, and the leakage is removed in time to avoid accumulation in the sealing part. The scheme is applicable to high-temperature hot oil pump with relatively clean transmission medium. Scheme 32 is external flushing and quenching at the back of stationary ring. External flushing is to inject the low-temperature clean cooling oil compatible with the pumped medium into the sealing chamber, cool the sealing elements directly, and remove the solid particles in the medium in time to avoid entering the sealing face or gathering near the seal to cause abrasive wear.
The statistical results show that the service life of the mechanical seal of the high-temperature oil pump can reach more than one year under the condition of ensuring the normal operation of the auxiliary system and the stable operation of the pump. However, with the continuous improvement of energy-saving and emission reduction requirements for modern industrial production, the performance of tubular mechanical seals and auxiliary systems can no longer meet the requirements, and the main problems exposed are:
① With the existing mechanical seal and its auxiliary system, the operation of high-temperature oil pump under variable working conditions often occurs. Pump evacuation, misoperation, artificial flow regulation, etc. make the mechanical seal under variable working conditions When the pressure of the sealed medium fluctuates violently, it can cause mutual impact of friction pairs, resulting in end face damage, thus affecting the sealing effect; If the operating pressure of the seal chamber fluctuates and becomes negative pressure instantaneously, the bellows shrinks and cannot be recovered in time, and the oil film seal formed between the dynamic and static ring friction pairs is damaged, resulting in sudden leakage failure.
② The temperature of the working medium is very high, plus the friction heat on the end face of the seal friction pair, once the flushing system fails, the end face temperature rises sharply, causing the end face liquid film to vaporize, leading to dry friction, which can make the seal fail in a short time; Secondly, high temperature can also reduce the performance of the graphite ring, and can melt the impregnating agent in serious cases; Thirdly, when tungsten carbide and graphite are used as the matching materials for the moving and stationary rings, the high temperature can also cause circular grooves on the surface of the graphite ring (stationary ring), and tungsten carbide (moving ring) is also easy to fall off; Finally, the thermal deformation of the friction pair is large at high temperature, which changes the end friction state. This led to premature failure of the sealing system.
③ High operation cost and large energy consumption. For the residue oil pump at the bottom of the atmospheric and vacuum tower, the external flushing scheme 32 is adopted, and the flushing liquid is directly fed into the process medium, which makes its consumption larger and the production cost higher. For example, for two bottom reducing pumps in the atmospheric and vacuum distillation unit of a plant, one pump has more than 20 tons of wax oil injected into the heavy oil residue system every day. If the price difference between heavy oil and wax oil is 1 ton, the daily economic loss is estimated to be 20 * 10 million=20000 yuan. The annual loss is 20000 yuan * 360=7.2 million yuan. Using the self flushing scheme 21 to cool the high temperature medium and then inject it into the pump will inevitably consume a lot of heat, reducing the efficiency of the pump. At the same time, the cooling water consumption is also quite large.
④ Both Scheme 21 and Scheme 32 need to put quench water into the back of the static ring of the mechanical seal for cooling, which is used to cool the friction pairs of the dynamic and static rings, so as to reduce the temperature between the bellows and the friction pairs to a certain extent, provide a suitable operating environment for the mechanical seal, prevent the deformation or failure of the mechanical seal components at high temperature, so as to improve the sealing effect and extend the service life. However, because the cooling water is scaling at the high temperature part, and the scaling is located between the friction pairs of the moving and stationary rings, the shaft sleeve that is close to them, and the wave plate of the bellows, the bellows will lose its elasticity and become invalid.
At present, bellows mechanical seal and its auxiliary system cause seal failure in the following forms:
(1) Seal failure caused by bellows loss of elasticity or fracture
During the use of bellows, its stiffness or elasticity will slowly decrease, and this phenomenon of elasticity reduction is usually called elastic loss. Experiments and practical applications show that when the elastic loss of bellows exceeds 18% - 20% of the design initial compression, the entire bellows mechanical seal will leak. Metal Corrugated pipe mechanical seal The elastic loss is not obvious when the temperature is lower than 200 ℃, but when the pump is used at high temperature (more than 300 ℃), the pump leaks soon after startup. When the used mechanical seal is removed from the measuring basin, it is found that the height of the metal bellows assembly is 2-3 mm lower than before installation. The elasticity loss of bellows is mainly due to permanent deformation or stress relaxation. In another case, the working medium crystallizes and settles or solidifies in the gap of bellows, reducing or losing the deformation capacity of bellows. Therefore, high temperature and load are the main reasons for the loss of elasticity of bellows.
In addition, under the condition of high temperature and large compression or contact specific pressure of bellows, the bellows will break (Figure 9-4); The higher the temperature and the greater the load, the higher the probability of bellows fracture.
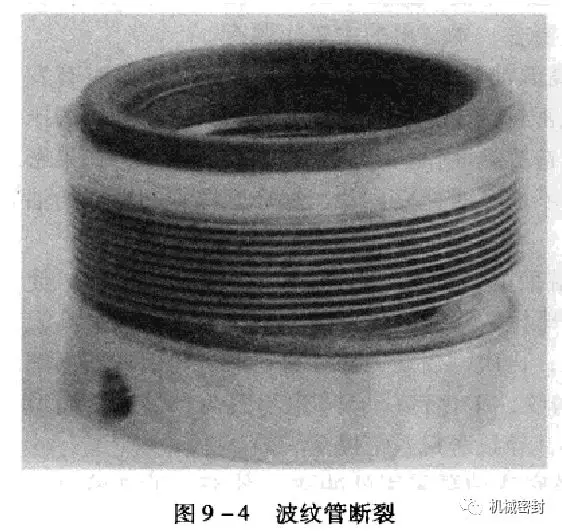
(2) Seal failure caused by excessive wear of graphite ring in paired friction pair
Generally, the graphite seal ring is severely worn after the failed mechanical seal is removed for inspection. Through analysis and test, it is found that the end face specific pressure of metal bellows mechanical seal is affected by the effective diameter of bellows, and the effective diameter changes with the change of pressure. When the bellows is subjected to external pressure, its effective diameter gradually decreases with the increase of pressure; When the bellows is subjected to internal pressure, its effective diameter gradually increases with the increase of pressure. Due to the excessive pressure, the friction pair is severely rubbed, and the graphite ring is excessively worn, causing leakage. Figure 9-5 shows the wear and abrasion of the graphite seal ring end face of the vacuum tower bottom pump in a plant.
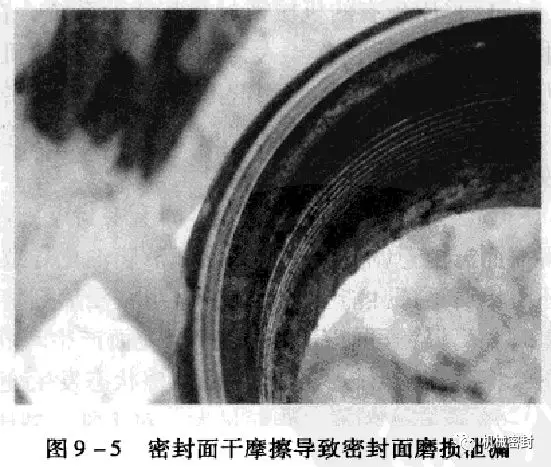
(3) Sealing failure caused by surface hot cracking of cemented carbide ring in paired friction pair
It was found that there were many radial cracks of different thickness in the cemented carbide ring of the friction pair. This is the seal failure caused by thermal cracking. The main reason for hot cracking is high local thermal stress. Among them, the difference of linear expansion coefficient between cemented carbide ring and ring seat materials, whether surfacing structure or integral structure is adopted, and whether the type, method and flow of flushing fluid in the seal cooling flushing system are suitable
It may cause hot cracking on the sealing face. Figure 9-6 shows that the mechanical seal end face of the vacuum tower bottom pump in a plant was suddenly filled with high temperature heavy oil, resulting in hot cracking of the seal surface and leakage.
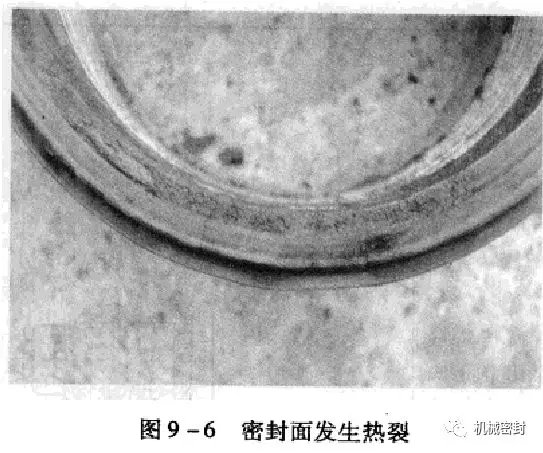