204 Mechanical seal The manufacturer teaches you how to prevent liquid pump leakage!
What should we do if the mechanical seal fluid pump leaks? Don't panic, Mechanical seal manufacturer To tell you how to solve the leakage, let's start with the basic elements of sealing:
Basic elements of sealing
Mechanical seal uses the principle that two planes rub against each other to achieve the purpose of sealing. The rotating sealing surface is installed on the main shaft of the liquid pump, while the fixed sealing surface is installed in the sealing gland. Since one sealing surface is moving while the other is stationary, this type of seal is called dynamic seal.
The latter two leakage paths are generally statically sealed because there is no relative movement between the two parts. This part of the seal is usually called tertiary seal, and its sealing material is gasket or O-ring suitable for the process fluid.
In the older seal design, the secondary seal under the rotating surface has a certain clearance, which can move back and forth on the main shaft, so it is easy to cause wear and premature failure. However, in the newer seal design, the secondary seal is in a static state, so wear and corrosion problems on the main shaft can be avoided.
During the normal operation of the liquid pump, the pressure generated by the liquid in the stuffing box between the rotating surface and the stationary surface keeps it in a sealed state. During the start and stop, the pressure of the stuffing box is maintained by the pressure generated by the spring (even can be replaced by the pressure of the spring).
Most mechanical seals are designed to use soft materials to make rotating surfaces, so that they can rotate and friction on a hard stationary surface. For many years, the most common combination is to use carbon material as the rotating surface to make it run on the ceramic stationary surface. This kind of material is still widely used, but the static surface is made of stainless steel or harder materials, such as tungsten carbide or silicon carbide.
No matter what materials are used, in short, a layer of liquid film must be kept between the contact surfaces to play the role of lubrication. However, in the stuffing box, the combination of spring load and liquid pressure can play a good sealing role between sealing faces. However, if the sealing pressure is too high
Influence the formation of liquid film between contact surfaces, resulting in increased heat and premature wear. If the sealing pressure is too low, the gap between the contact surfaces will increase, which is easy to cause liquid leakage.
The seal manufacturer is making continuous efforts to improve the flatness of the contact surface, and they use special polishing plates for grinding. Then, the grating plate with monochromatic light source is used to detect it. From this point of view, it is very important to carefully handle these sealing contact surfaces and strictly follow the installation instructions to ensure that the sealing surfaces are properly protected and correctly positioned.
Flexible selection of seals
The axial and radial movements of the spindle need to maintain a certain flexibility with the spring to ensure the sealing between the contact surfaces. However, only a certain degree of flexibility can be provided. The mechanical condition of the liquid pump and its length diameter ratio (a measure of the ratio of the diameter of the main shaft to its extension length, the lower the ratio, the better) play an important role in the reliability of the seal. The flexibility of the seal is generally guaranteed by a large main spring and a series of small springs or corrugated seals.
The traditional seal design used in the chemical industry, whose sealing pressure is applied to the rotating surface, is called a rotary seal because the spring or corrugated seal device rotates with the main shaft. The spring or corrugated sealing device of the novel design is installed on the static surface. On the current mechanical seal, the two sealing methods mentioned above are very common, which has certain flexibility for installation.
Many mechanical seals designed in the early stage use a single large spring arranged around the main shaft, which can provide a strong sealing force for the sealing surface during the starting process of the liquid pump. The sealing function relies on the rotation of the main shaft to tension the spring coil.
For many corrosive application fields, the most common design is to use metal bellows sealing device. The bellows is welded by a series of metal discs to form a corrugated sealing device to prevent leakage. Using this device can make the sealing pressure between sealing surfaces more uniform, and there is no need to add a secondary seal on the sealing surface, so that no corrosion and wear will occur naturally.
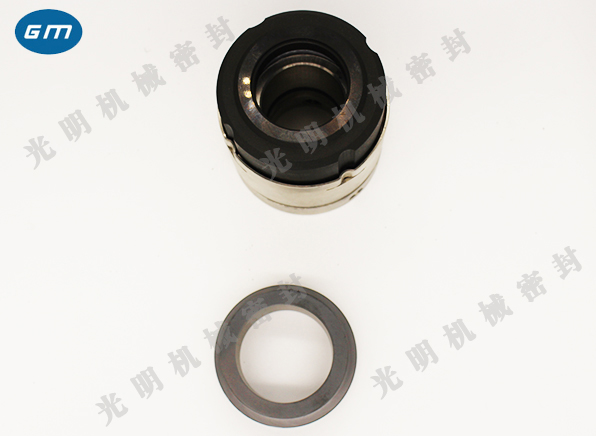
Generally speaking, although its main sealing pressure depends on the pressure of the stuffing box itself, the spring and bellows can compensate for the insufficient pressure of the main shaft movement during the startup and shutdown of the liquid pump, so that the sealing surface always maintains a certain sealing pressure.
Corrosion and wear problems
Due to various reasons, such as bearing tolerance, shaft end clearance, vibration and spindle deviation, the spindle of the hydraulic pump will produce radial and axial movement. In addition, it is very difficult to keep the contact surfaces absolutely parallel, so it is normal for the internal movement of the mechanical seal itself. This kind of movement is often caused by improper adjustment of equipment and installation tolerance, thermal expansion, pipeline stress or main shaft.
In order to keep the sealing surfaces matching each other all the time, the spring plays a constant regulating role between the mechanical seal and the moving spindle. When the artificial rubber seal is used between the rotating surface and the main shaft, the elastomer will move back and forth on the main shaft. This repeated friction action will abrade the anti-corrosion materials on the main shaft, lose the oxide film protective layer of the main shaft, and eventually form a wear groove on the friction surface of the main shaft, causing liquid leakage from the groove, and increasing the necessary maintenance workload or even replacing the main shaft. To solve this problem, a replaceable shaft sleeve is usually installed in the stuffing box.
However, the only permanent solution to the problem of corrosive wear is to remove the dynamic seal inside. At present, most major seal manufacturers produce non corrosive wear type seals to prevent corrosive wear of liquid pump parts.