Mechanical seal manufacturer Tell you the precise selection and application of mechanical seal for solid-liquid two-phase flow pump?
Due to the existence of abrasive particle media in solid-liquid two-phase flow, the following five hazards are often caused by the selection of general mechanical seals:
① Increased wear of seal face. Between the sealing surfaces, because of the leakage of separated mechanical sealing particles used by the pump into the end face, they play an abrasive role and accelerate the wear of the sealing surface.
② Particles on the medium side are blocked. Due to the accumulation of particles, bridging is obstructed for the spring and pin pump Cartridge mechanical seal And assisting in the movement of the sealing ring, which then leads to the decline of the compliance and buoyancy of the compensation ring.
③ Particle blockage at the atmospheric side. Due to the conventional planned mechanical seal, the space between the inner diameter of the sealing surface and the shaft (or shaft sleeve) is small, and the leaked solid particles cannot be discharged in time, which is easy to accumulate and block, blocking the movement of the auxiliary seal ring, and then leading to the failure of the seal.
④ Abrasion. It refers to the partial erosion and tearing of the seal element surface due to the effect of abrasive printing and dyeing mechanical seal particles. It is generally formed due to the impact of scouring water or sealing liquid when using softer steel or graphite materials. In the case of granular media, the attack becomes more serious;
⑤ Wear of transmission elements. Because these elements of the drive pin are in the granular medium, the abrasion of the elements themselves is aggravated due to the abrasive action of the particles during the movement.
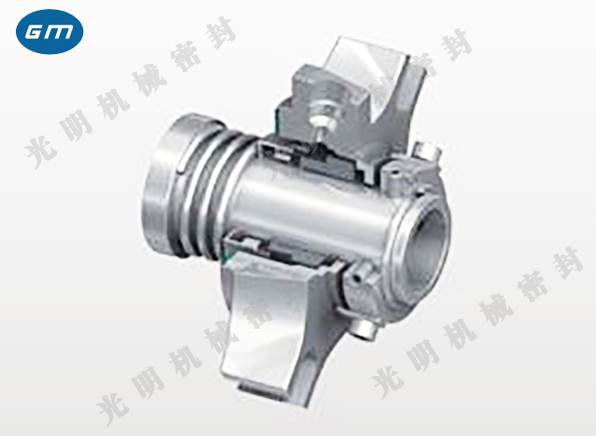
When selecting the model, the mechanical seal products should avoid the effect of particles as much as possible to avoid these five failures. There are two ways for the mechanical seal to deal with the problem of the role of particle media: one is to set some additional internal structures for the mechanical seal or use auxiliary methods (such as spiral seal, lip seal, sealing liquid, flushing water, water tank or oil tank to set up a liquid barrier to avoid particle accumulation, etc.), Maybe external equipment (such as cyclone solid-liquid separator, magnetic filter, etc.) should try to avoid the above five failures to protect the outstanding working condition of mechanical seal. This way refers to the primary occasions, and the primary equipment can be used. However, due to space constraints, perhaps due to the high consumption of auxiliary equipment, and due to some situations where materials are not allowed to have sealing fluid or flushing water entering the product, a new type of mechanical seal structure should be selected and planned, which can be directly used in granular media, satisfying the requirements of the production process for sealing.
In order to achieve the purpose of reliable seal, long life, simple structure, convenient assembly and disassembly, easy dispatching and low cost, the specific methods are as follows:
Spring and auxiliary seal ring are used together. The primary benefit is that it has high elasticity, and the spring does not touch the medium, avoiding the question of being easily blocked by particles.
In order to ensure that the resistance pair has the purpose of wear and corrosion resistance in granular media, the hardness of the resistance pair material must be higher than that of the abrasive particles. Generally, hard to hard pairing can be selected, and the raw materials can be tungsten carbide or silicon carbide. Compared with tungsten carbide, silicon carbide has higher hardness, very good thermal conductivity, good chemical stability and self-lubricating property, but its cost is high.
According to A 1. GoLubiev (the former Soviet Union) and others concluded from their research on the wear mechanism of high hardness resistance pairs in abrasive granular media that the width of resistance pairs should be wider than that of general mechanical seals to obtain a higher service life. The rotating and stationary rings have the same width, which is conducive to avoiding the wear of particles on the sealing face. Together, they have a satisfactory area to avoid large mismatches. Therefore, the radial and axial runout can be much larger than that of the general mechanical seal face.
The mechanical seal for mixed flow pump shall be designed as an internal flow type. The granular medium is outside the seal ring. The centrifugal force and inertial force make the particles and impurities move outward and throw away from the sealing surface.
Different from general mechanical seals, the space between the shaft sleeve and the seal ring should be large. When there is material leakage, it can be discharged in time to avoid the accumulation and blockage of particles. It is necessary to have proper space for the plan of the sealing chamber, so that the materials in the sealing chamber can move, do not accumulate and deposit, and are easy to cool and lubricate the seal. In order to reduce the influence of the medium pressure in the pump on the specific pressure of the seal face, the balanced mechanical seal structure is selected.
The end face pressure is one of the most important factors affecting the function and service life of seals. In order to prevent the granular medium from entering the seal face, the leakage will increase, and the wear of the face will increase, leading to the failure of the seal, the specific pressure of the face should be larger than that of the general. However, if the end face specific pressure is too large, the heat and wear of the contact surface will be intensified, and the power consumption will be increased. When planning, the end face specific pressure is 0.3 MPa.
When single end mechanical seal is selected, washing, filtering, separation, isolation, heat preservation and heating methods shall be adopted according to different conditions to avoid the harm of particle impurities. The reliability and quality of the flushing fluid is the key to the success of sealing. If the flushing fluid is written from the outside, the working environment of the seal can be improved, but it is necessary to consume the flushing fluid, and the prerequisite is that the conveyed fluid is allowed to be slightly diluted by the flushing fluid.
When double end mechanical seal is selected, the sealing fluid is requested to set up pressure in the sealing cavity for sealing, lubrication and cooling circulation. The double end face seal has high reliability, but the forming cost and equipment cost are high. The selection of materials for most double face seal groups has been standardized. In practical application, the resistance pair at the medium end is matched with cemented carbide or silicon carbide; The carbon graphite and nickel chromium steel at the atmospheric end shall be matched.