204 Mechanical seal manufacturer Introduce the installation and maintenance of pump mechanical seal
1 Installation of pump mechanical seal
1.1 Preparation for installation of pump mechanical seal
Make sure that the mounting chamber is clean and free of any foreign matter. The shaft or sleeve matched with the mechanical seal shall have correct size, smooth surface, good mechanical seal for linear pump, and no burr, sharp corner, nick or too deep scratch. Seal all holes in the seal chamber that are not used by the mechanical seal during operation. The end face of the seal chamber must be clean, smooth and perpendicular to the axis line. The two boxes of the horizontal split pump must be well matched. There are sealing gaskets between the two boxes. Remove all sharp corners and burrs on the surface of the sealing chamber.
Check the alignment of the shaft with a dial indicator. In order to obtain the best sealing performance, the maximum allowable error of shaft alignment is 0.125mm (total indicated deviation). Excessive misalignment may mean that there are damaged bearings or bent shafts. Keep the shaft displacement to be minimum, and the recommended displacement range is 0.125mm. Check between the wear ring and the impeller of the pump Mechanical seal for kettle Whether the clearance is proper, the shaft must rotate freely, and the vibration caused by friction and improper clearance can cause seal damage. When using the shaft sleeve, ensure that the shaft sleeve is properly sealed on the shaft to prevent leakage under the shaft sleeve.
1.2 Seal installation
(1) Mechanical seal shall be handled carefully. It is important to be clean. Do not put the seal face down on the ground or chair. Carefully read and follow the seal installation instructions provided by the manufacturer. Do not unpack until ready for installation.
(2) Ensure that all mounting screws are fastened. When the mounting screw is used as the drive between the seal and the shaft, the shaft shall be countersunk to strengthen the connection. When tightening the gland bolts, they should be tightened steadily and the gland should not be subject to elastic force. Use equally spaced glands with more than 4 screws where possible. When tightening the gland bolts, check the clearance between the shaft and the gland with a feeler gauge, which is particularly important when the seal chamber is not guided to the gland, because the gland must be accurately aligned.
⑶ Before starting the pump, test the seal statically under pressure, and slightly adjust the gland nut to prevent possible leakage at the gland gasket.
⑷ Do not run the mechanical seal dry. In certain cases, the manufacturer's operating instructions should be followed for flushing and cooling connections. Ensure that the suction and discharge ports of the pump are open, and there is a positive liquid level pressure before starting the pump. When checking whether the rotation direction is correct and adjusting the connection of the motor, do the same.
2 Maintenance analysis of pump machinery
Effective maintenance analysis requires the ability to observe the change of sealing performance in a certain period of time, and to thoroughly investigate the cause of failure and take countermeasures in case of failure.
(1) Blowout and bursting of seals during operation. Since vaporizable pumpers flash when passing through sealing surfaces, this requires specific liquid conditions between surfaces and maintains these conditions. Check whether some pressure needs balanced design instead of unbalanced design. If the seal has been balanced, the pressure may have seriously exceeded the value specified in the instructions. Determine the correct actual stuffing box pressure, temperature and material specific gravity, as well as the vaporization pressure of the processed product in these cases, because these data may provide clues for troubleshooting.
(2) Seal leakage and icing around the gland. Due to vaporization, the product flashes when passing through the sealing surface. If it freezes, there must be no doubt that there must be damage on the static seal and carbon seal ring. If possible, these surfaces shall be inspected and repaired, and replaced after the vaporization conditions are changed if necessary.
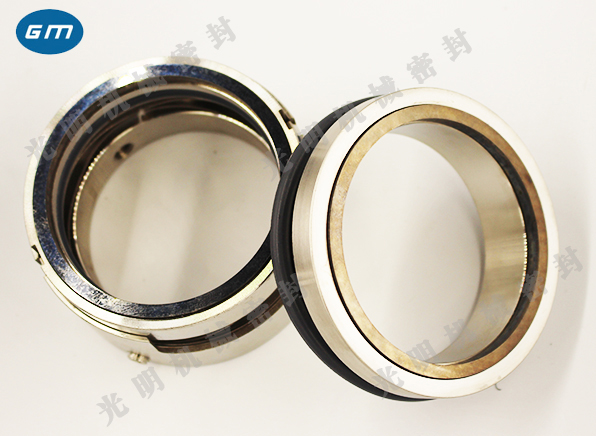
⑶ Seal and drip stably. Check whether the pressure of the gland gasket on the stuffing box surface is abnormal. For the pump with horizontal split casing, check the sealing of the connection surface and gland. The gland surface may be deformed or uneven. Improper distribution of gland bolts or too tight bolt force may cause deformation of static seal, which mainly occurs on edge fixed type seals.
During installation, the contact part of the shaft on the rotating part or stationary ring seal may be damaged. The wear surface may be caused by abrasive particles or other particles. If the seal is assembled as a whole or installed on the pump sleeve, the leakage may come out from under the shaft sleeve. Note that sometimes the new seal leaks when it is just put into use, but the leakage will gradually decrease after several hours of operation.
(4) Seal vibrating sound. The seal ringing indicates that the seal may be in dry operation without liquid lubrication. It may also be necessary to introduce a circulating flushing pipe from the drain or an external liquid source. If one has been installed, the hole may be too small.
(5) There is powder on the rotating surface, which is displayed on the outside of the seal on the gland and along the shaft. There is not enough liquid on the sealing surface. Due to the flashing of vaporized liquid, small residual crystalline particles are left between the seals, or dry contact is generated, resulting in grinding. From the design of the seal, it is obvious that the pressure of the seal chamber is too high, and re balancing the seal pressure may be the answer.
(6) There is seal leakage and no obvious fault here. The surface may be uneven, which can be determined by removing it and checking the wear pattern, or the deformation of the static seal may be caused by the excessive pressure of the gland bolt clamping the static seal and bending at the same time. This can also be determined by checking the wear pattern. Inappropriate pipelines connected to the outlet and inlet of the pump can actually stress the pump, and the sealing surface may also be bent during shaft alignment.
(7) Short sealing life. The main reason for the short life of the seal is that there is too much friction between the faces and fast wear. The friction source may come from mud, or from the quench of supersaturated solution, or from the flash evaporation of liquid between sealing surfaces, causing the crystallization of dissolved solids between surfaces. When this happens, cooling or heating to ensure the circulation of pump fluid from the discharge port to the stuffing box or external clean flushing will alleviate these conditions.
(8) Equipment dislocation and connecting pipe stress bending. When the seal shows overheating, bypass flushing or circulation may be required. Check the sealing elements along the shaft for possible wear. These conditions can often be caused by intercepting bushings and poor guide glands. Check all flushing pipelines and through holes to ensure that they are smooth, clean and free of blockage. Reduce heat by increasing the capacity of cooling pipelines or expanding the size of holes on circulating pipelines. In addition, it is also possible that improper seal type has been selected.