204 Mechanical seal manufacturer Introduce basic knowledge
Basic knowledge
1. Basic concept of mechanical seal:
Mechanical seal refers to a device to prevent fluid leakage, which is composed of at least one pair of end faces perpendicular to the rotation axis under the action of fluid pressure and the elastic force (or magnetic force) of the compensation mechanism, and with the cooperation of the auxiliary seal. The auxiliary seal of compensation ring is metal bellows, which is called bellows mechanical seal.
2. Composition of mechanical seal:
There are four main types of components. a. Main seals: dynamic ring and static ring. b. Auxiliary seal: seal ring. c. Compression parts: spring, push ring. d. Transmission part: skip seat and key or fixing screw
Attention
1. Precautions during installation
a. Pay great attention to avoid installation deviation during installation
(1) The gland shall be tightened after the alignment of the coupling. The bolts shall be evenly supported to prevent the end face of the gland from deflecting. Check each point with a feeler gauge, and the error shall not be greater than 0.05 mm.
(2) Check the fit clearance (i.e. concentricity) between the gland and the outer diameter of the shaft or shaft sleeve. The circumference should be even. Use a feeler gauge to check that the tolerance of each point is not more than 0.01mm.
b. The spring compression shall be carried out according to the regulations, and it is not allowed to be too large or too small. The required error is 2.00mm. If it is too large, the end face pressure will be increased, and the end face will be worn at another speed. If it is too small, the specific pressure will be insufficient and the sealing effect will not be achieved.
c. The movable ring shall be able to move flexibly on the shaft after installation, and it shall spring back automatically after pressing the movable ring against the spring.
2. Precautions during disassembly
a. When disassembling the mechanical seal, be careful. Never use a hammer or flat shovel to avoid damaging the sealing elements. It can be used as a pair of steel wire hooks to extend into the notch of the transmission seat in the direction of self financing and pull out the sealing device. If scaling cannot be removed, it shall be cleaned before removal.
b. If mechanical seals are used at both ends of the pump, take care of each other during assembly and disassembly to prevent neglect of one thing and loss of another.
c. For the operated mechanical seal, if the gland is loose and the seal moves, the moving and stationary ring parts must be replaced and should not be tightened again for further use. Because the original running track of the friction pair will change after the sample movement, the sealing of the contact surface will be easily damaged.
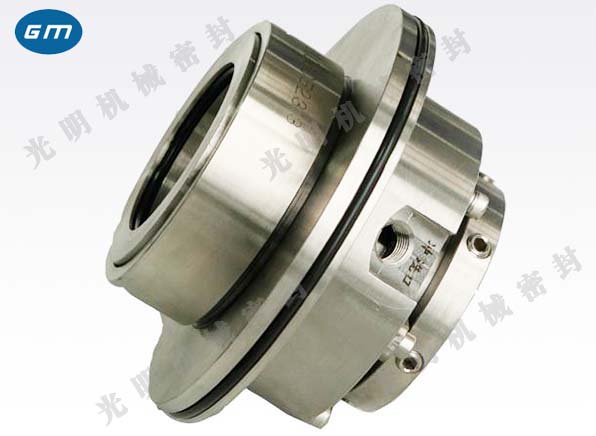
Normal operation and maintenance
1. Preparations and precautions before startup
a. Comprehensively check whether the mechanical seal, accessory devices and pipeline installation are complete and meet the technical requirements.
b. Static pressure test shall be carried out before starting the mechanical seal to check whether there is leakage of the mechanical seal. If there are many leaks, find out the causes and try to eliminate them. If it is still invalid, it shall be disassembled, checked and reinstalled. The general hydrostatic test pressure is 2~3 kg/cm2.
c. Turn the gear according to the rotation direction of the pump and check whether it is light and even. If the turning gear is hard or does not move, check whether the assembly size is wrong and the installation is reasonable.
2. Installation and shutdown
a. The sealing chamber shall be kept full of liquid before starting. When transporting solidified medium, the sealing chamber shall be heated by steam to melt the medium. The turning gear must be turned before starting to prevent the soft ring from breaking due to sudden starting.
b. For the mechanical seal using the external sealing oil system of the pump, the sealing oil system shall be started first. Finally stop the oil sealing system after shutdown.
c. After the hot oil pump is shut down, the cooling water of the seal oil chamber and the end face seal cannot be stopped immediately. The cooling water can only be stopped when the oil temperature at the end face seal drops below 80 degrees to avoid damaging the sealing parts.
3. Operation
a. If there is slight leakage after the pump is started, observe for a period of time. If the leakage does not decrease after 4 hours of continuous operation, stop the pump for inspection.
b. The operating pressure of the pump shall be stable, and the pressure fluctuation shall not exceed 1kg/cm2.
c. During the operation of the pump, evacuation shall be avoided to avoid dry friction on the sealing surface and seal damage.
d. The sealing condition shall be checked frequently. During operation, when the leakage exceeds the standard, the heavy oil shall not be more than 5 drops/min and the light oil shall not be more than 10/min. If there is no improvement trend within 2-3 days, the pump shall be stopped and the sealing device shall be checked.
The development of "seal" in China has a long history. The ancients used cotton, hemp and other fibers as the seals of water lifting machinery, while foreign countries only used filler in 1782. The importance of sealing will not be mentioned here. Now there has been a discipline of studying sealing laws, sealing device design technology and applied scientific principles abroad - "sealing science". Scientific research institutions also have professional courses specialized in sealing science. In China, so far, as far as I know, there are courses of fluid mechanics and hydraulic transmission in universities, However, there is no "sealing system" specialized in sealing, so our research level is still lagging behind that of foreign countries.