Features of reactor sealing device
Understanding the characteristics of different types of reactors can help us master the key points of mechanical seal design.
1. Stirring shaft side plug-in reactor
From the lubrication point of view, this kind of reaction Mechanical seal for kettle Generally, poor lubrication will not occur, and the liquid level of the medium in the kettle must be kept at a certain height. For the reaction kettle with the shaft protruding from one side, the shaft is in a cantilever state, so it is easy to generate vibration, while the mechanical seal is more sensitive to vibration. If the shaft extends from both sides, the shaft must be aligned with the support device on the kettle body, which is difficult to meet this requirement, so the balance between the shaft and the kettle is very complex. When the operating temperature changes greatly, the expansion and contraction of the shaft is large. If the excessive expansion and contraction are all borne by the mechanical seal, the mechanical seal is easy to fail. However, the rotating speed of this type of kettle is not high, and this problem can be solved by taking corresponding measures.
2. Inserted reaction kettle at the bottom of mixing shaft
Polymerization reactor has gradually developed towards large volume, and its stirring shaft has also changed from top inserted type to bottom inserted type. The bottom plug-in reactor is characterized by short mixing shaft and small bending stress on the shaft, so the calculated shaft diameter is small, saving labor and materials. The short axis is more rigid than the long axis and has less deformation. However, the seal is located at the bottom of the kettle. Although it can ensure the lubrication of the seal, solid impurities are easy to deposit around the seal, causing abrasive wear on the friction end face and blocking and scaling of moving parts. In this case, the mechanical seal is always subject to the pressure of the liquid. When the seal needs to be repaired or replaced, the materials in the kettle must be emptied. When the material is a polymer with high viscosity, it is difficult to completely empty it. Therefore, it is necessary to carry out special design for mechanical seal and take special measures at the same time, so that the seal can be expected to have good working performance and be convenient for maintenance.
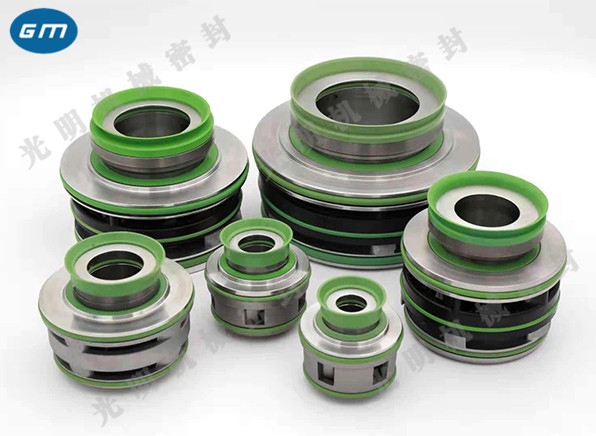
3. Plug in reactor at the top of mixing shaft
The top inserted stirring shaft reactor is widely used, and its sealing problems are different from those mentioned above.
① Since the seal is placed on the upper part of the kettle, in the gas phase space (the liquid phase is only when the kettle is full of materials), the medium sealed by the kettle mechanical seal is mostly gas rather than liquid. In this way, from the working condition of the seal face, compared with the pump seal, the lubrication condition is poor, and it is easy to be in a dry friction state, resulting in end face wear. Therefore, certain lubrication and cooling methods need to be adopted. At the same time, due to the strong gas leakage, for materials with large porosity such as graphite rings, in addition to hydraulic test, the requirements for air tightness test should be increased.
② Due to the change of process conditions, the pressure and temperature of reaction kettle are not always constant and fluctuate frequently. Therefore, the design shall ensure that the operating requirements can also be met when the pressure fluctuates (high pressure operation, low pressure operation and vacuum operation).
③ The top is inserted with a vertically installed mixing shaft, and the lower end is equipped with a mixing shaft, which is often in a cantilever state. Due to the large length diameter ratio, it is difficult to ensure the processing and installation accuracy, and it is easy to produce large deflection. During operation, the mixing blades are uneven; The liquid level is too low or there is an accident flow; The feeding is uneven, or the reaction is not well controlled; Pressure and temperature fluctuations; Pressure and temperature changes cause deformation of mixing shaft and kettle body; Sudden changes in the speed of the mixing shaft, or factors such as the increase in polymer viscosity caused by cooling, will intensify the vibration of the mixing shaft. To solve this problem, provide a
Relative to the working environment without vibration, to make the seal run smoothly, it is generally necessary to take measures such as intermediate bearing and bottom bearing to limit, so as to minimize the impact of shaft vibration on seal performance. Therefore, the requirement of the mechanical seal for kettle on the radial runout of shaft is much worse than that of the mechanical seal for pump. When the shaft diameter is} 65mm, the radial runout is less than 0.5mm; When the shaft diameter is>65mm, the radial runout is<1mm; At the same time, the dynamic ring and the static ring should have better floatability and tracking property when designing.
④ The mechanical seal for kettle is usually used at large diameter and low rotating speed. With the development of scientific research and production, the reactor device tends to be large-scale. The volume of the kettle keeps increasing, and the diameter of the mixing shaft has exceeded 300mm. However, the rotating speed of the mixing shaft is generally low, generally below 200.300 r/min, and the high use range is 500 r/min. When the diameter is large, it is easy to cause deformation of the seal ring, and it is difficult to ensure the flatness of the seal face. When the diameter is large, the hard sealing ring often uses surface composite materials.
⑤ Due to the large size, heavy parts and complicated replacement, the mechanical seal for kettle should be designed to be easy and simple to assemble and disassemble. Generally, low parameter kettles are mainly installed outside of the seal. For high parameter reactors and large reactors, mechanical seal parts need to be installed on the reactors one by one, and it is difficult to ensure their accuracy. Many failures of mechanical seals for kettles are caused by poor installation. At this time, the mechanical seal is often designed as a combined container, and the mechanical seal, shaft sleeve, cooling and flushing jacket, gland and flange are assembled as a combination, and are installed on the kettle together after debugging in the workshop, without further adjustment; During maintenance, the spare seal shall also be removed and installed as a whole. The repair and replacement of the old assembly can be carried out in the maintenance workshop. In this way, the installation and maintenance process of the seal is greatly accelerated, thus avoiding installation errors and reducing downtime losses in production.