Mechanical seal for kettle The manufacturer introduces the leakage point of chemical pump
There are many kinds of mechanical seals for pumps with different models, but there are mainly five leakage points:
Seal between shaft sleeve and shaft
Seal between moving ring and shaft sleeve
Seal between dynamic and static rings
Sealing between stationary ring and stationary ring seat
Seal between seal end cover and pump body
Phenomenon: the seal makes a popping sound (end face popping sound) during operation
Possible causes: the sealing liquid vaporizes at the sealing interface; Strengthen cooling of sealing surface
Solution: Add bypass flushing pipeline (if not available) and expand the opening on bypass flushing pipeline and/or gland.
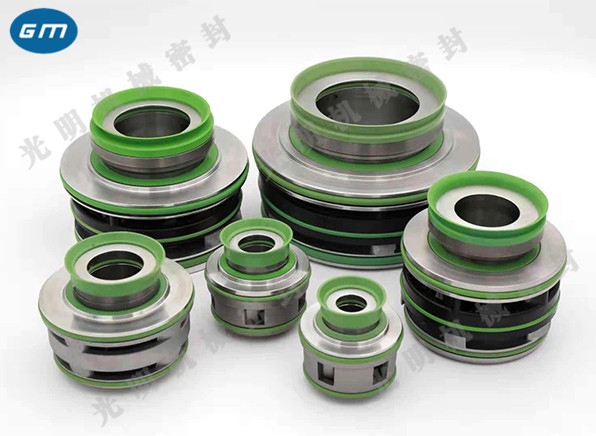
Phenomenon: continuous leakage of sealing
Possible causes: uneven surface; The graphite sealing surface bubbles; Thermal deformation of sealing surface
Solution: During installation, the auxiliary seal was scratched and the O-ring was aged. Due to compression deformation, the auxiliary seal became hard and brittle. Due to chemical action, the auxiliary seal became soft and sticky.
Phenomenon: spring failure
Possible causes: due to corrosion, metal accessories are damaged and transmission mechanism is corroded
Solution: check the incorrect installation size, check whether the inappropriate materials and seal types are used to improve the flushing cooling pipeline, check whether the gland bolt torque is too large, which leads to the deformation of the gland, check whether the specific pressure of the gland gasket is appropriate, check whether there are other solid particles between the sealing surfaces, and re polish the sealing surface if necessary. Check the cracks on the sealing surface and replace the main and matching sealing rings.
Phenomenon: During operation, the seal emits a squealing sound
Possible cause: insufficient lubricant at the seal
Solution: Add bypass flushing pipeline (if not available) and expand the opening on bypass flushing pipeline and/or gland.