Mechanical seal manufacturer Introduce typical fault types and properties
Mechanical seal damage types include chemical damage, thermal damage and mechanical damage.
(1) Chemical damage
1) Surface corrosion If the metal surface contacts the corrosive medium, but the metal itself does not corrode, surface corrosion will occur. In order to prevent surface corrosion, corrosion resistant materials can be used. The corrosion resistance of stainless steel is good, because the protective film of oxide or hydroxide is formed on the surface at this time, so that the metal is passivated without corrosion.
2) Pitting The severe corrosion spots on the surface of metal materials are called pitting corrosion. Generally, there are two types of pitting: pitting on the whole surface and pitting on the local surface. When stainless steel is used, pitting corrosion will occur when the passivated chromium oxide protective film is partially damaged. The way to prevent it is to limit the chromium content in the metal composition and add nickel and copper. Pitting is more dangerous than uniform corrosion.
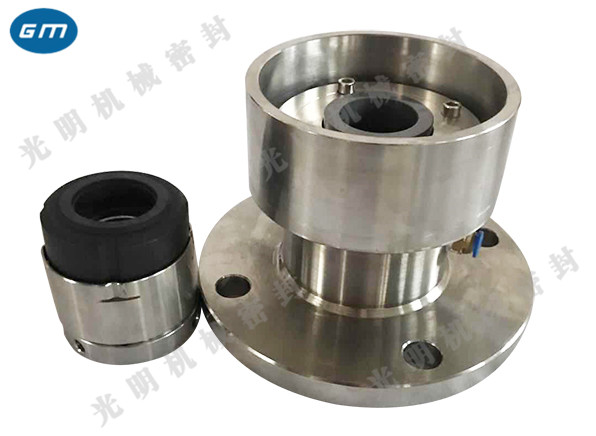
3) Intergranular corrosion intergranular corrosion is a severe corrosion phenomenon that only occurs at the crystal interface of metal. Although its weight corrosion rate is very small, it can deeply corrode the inside of the metal, and also cause cutting damage due to notch effect. For austenitic stainless steel, intergranular corrosion occurs at 450~850 ℃, and chromium carbide precipitates at the grain boundary, which makes the material lose its inertia and cause intergranular corrosion. In order to prevent this corrosion, the material shall be heat treated at 1050 ℃ to make chromium solid melt and evenly distributed in the austenitic matrix.
4) Stress corrosion The corrosion phenomenon that occurs when metal materials are in a corrosive environment under stress. The materials prone to stress corrosion are aluminum alloy, copper alloy, steel and austenitic stainless steel. Generally, stress corrosion occurs under high tensile stress, which first shows as groove marks, cracks, and finally completely breaks.
5) Crevice corrosion Crevice corrosion is a kind of concentration cell corrosion, which occurs in the narrow gap between two parts. This corrosion phenomenon can often be observed near the O-ring of mechanical seal. This is because the medium flow is blocked by the narrow gap and forms an inert oxide layer. The solution in the narrow gap forms a concentration cell with the solution outside the gap due to insufficient oxygen supply, which causes corrosion in the gap.
6) Battery corrosion This is due to the potential difference between the two metals in the dielectric solution, resulting in battery action and battery corrosion. In order to prevent battery corrosion, try to avoid using the structure of two metal combinations with potential difference. The battery voltage sequence of some metals is shown in the following table:
Electrolyte: 3% NaCI solution of natural seawater at 25 ℃.
7) Compared with the above chemical corrosion and electrochemical corrosion, cavitation and erosion are mostly mechanical factors. Metal materials in high-speed motion are often accompanied by corrosion due to cavitation.