Some Key Points of Mechanical Seal Installation and Disassembly
There should be a layer of liquid film between the sealing rings of mechanical seal, which has the following functions:
1. Support most of the water pressure load on the seal.
2. As a lubricant, reduce the friction heat generated by the seal ring.
3. Minimize rough contact to reduce wear rate.
4. As the heat transfer medium, transfer the heat energy in the direct area of the seal ring.
Before we disassemble the mechanical seal, we should first think about the following points:
1. Where is the main leakage?
2. Is there any debris on the external parts?
3. Is eccentricity of shaft or rotating sealing parts observed?
4. Is there any vibration/noise related to the system (such as cavitation and dislocation)?
5. Is there local heat generation in the "pump" or seal?
6. Is the leakage intermittent under different conditions, such as different temperatures?
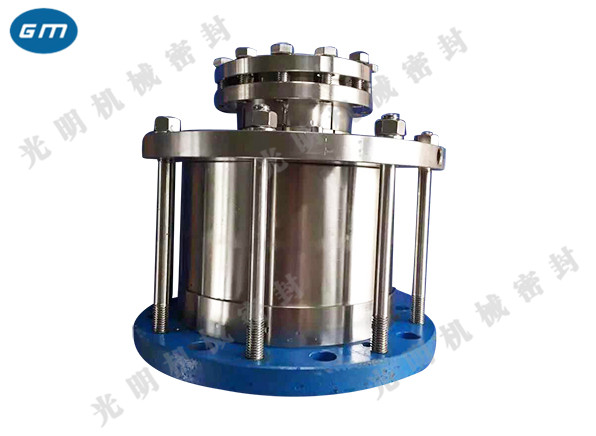
7. What kind of leakage, spray, droplet, water flow or flow to the pipeline?
8. Does the bearing have axial clearance?
9. If it is a double face seal, check whether the isolating fluid supply is intact.
10. Relative position of seal on shaft?
In the process of removing the seal, we should pay attention to the following points:
1. Status of gasket and running in end face?
2. Shaft condition and size?
3. Blocking/sealing cavitation of the machine?
4. Is it loose or tight when it is installed on the shaft?
5. Corrosion of the machine?
6. Is there any sealing debris in the machine?
7. Is there a reference mark where the seal is installed on the shaft?
8. Relative hardness of shaft at sealing position?
When removing the seal, we should pay attention to the following points:
1. During the removal process, great care must be taken to prevent any damage from covering up the real cause of the original seal failure;
3. Pay attention to observation and make records when removing parts, and then remove the next part;
4. The observed faults must be classified, such as wear, dry running, sealing ring emitting sound, etc.
Installation of mechanical seal
Make sure that the mounting chamber is clean and free of any foreign matter. The shaft or sleeve matched with the mechanical seal shall be of correct size, smooth surface, good straightness, and free from burrs, sharp corners, nicks or deep scratches. Seal all holes in the seal chamber that are not used by the mechanical seal during operation. The end face of the seal chamber must be clean, smooth and perpendicular to the axis line. The two boxes of the horizontal split pump must be well matched. There are sealing gaskets between the two boxes. Remove all sharp corners and burrs on the surface of the sealing chamber.
Check whether the clearance between the wear ring and the impeller of the pump is proper, the shaft must rotate freely, and the vibration caused by friction and improper clearance can lead to seal damage. When using the shaft sleeve, ensure that the shaft sleeve is properly sealed on the shaft to prevent leakage under the shaft sleeve.
Ensure that all mounting screws are tight. When the mounting screw is used as the drive between the seal and the shaft, the shaft shall be countersunk to strengthen the connection. When tightening the gland bolts, they should be tightened steadily and the gland should not be subject to elastic force. Use equally spaced glands with more than 4 screws where possible. When tightening the gland bolts, check the clearance between the shaft and the gland with a feeler gauge, which is particularly important when the seal chamber is not guided to the gland, because the gland must be accurately aligned.
Before starting the pump, statically test the seal under pressure, and slightly adjust the gland nut to prevent possible leakage at the gland gasket.
Do not run the mechanical seal dry. In certain cases, the manufacturer's operating instructions should be followed for flushing and cooling connections. Ensure that the suction and discharge ports of the pump are open, and there is a positive liquid level pressure before starting the pump. When checking whether the rotation direction is correct and adjusting the connection of the motor, do the same.
Check whether the model, specification and quantity of the mechanical seal meet the requirements of the design drawings, and whether all parts (especially the sealing surface and auxiliary sealing ring) are damaged, deformed, cracked, etc. If there are defects, they must be replaced or repaired.