Mechanical seal for kettle Lubrication of
Mechanical seals working in liquid medium generally rely on the liquid film formed by the liquid medium between the moving and stationary ring friction surfaces for lubrication. Therefore, maintaining the liquid film between friction surfaces is essential to ensure the stable operation of mechanical seals and extend their service life.
According to different conditions, the friction between the dynamic and static rings of the mechanical seal may occur in the following situations:
(1) Dry friction:
There is no liquid entering the sliding friction surface, so there is no liquid film, only dust, oxide layer, and adsorbed gas molecules. When the dynamic and static rings are running, the result must be that the friction surface heats up and the wear intensifies, resulting in leakage.
(2) Boundary lubrication:
When the pressure between the moving and stationary rings increases or the ability of the liquid to form a liquid film on the friction surface is poor, the liquid will be squeezed out of the gap. Because the surface is not absolutely flat, but uneven, there is contact wear in the bulge, while the lubrication performance of the liquid is maintained in the concave, resulting in boundary lubrication. The wear and heat of boundary lubrication is medium.
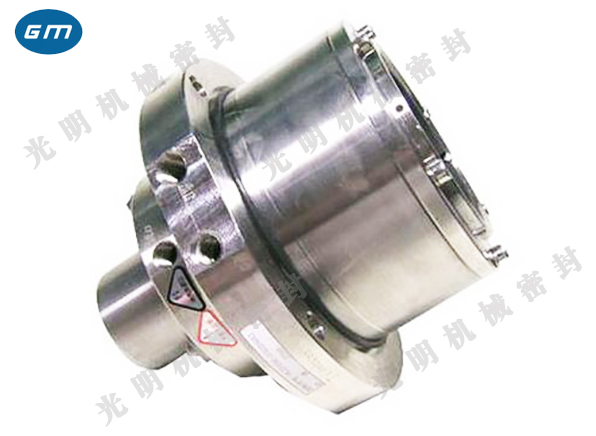
(3) Semi liquid lubrication:
There is liquid in the pit of the sliding surface, and a thin liquid film is maintained between the contact surfaces, so the heating and wear conditions are good. Because the liquid film between the moving and stationary rings has surface tension at its outlet, the leakage of liquid is limited.
(4) Fully liquid lubricated:
When the pressure between the moving and stationary rings is insufficient and the gap increases, the liquid film thickens. At this time, there is no solid contact, so there is no friction phenomenon. However, in this case, the gap between the moving and stationary rings is large, so it can not play a sealing role, and the leakage is serious. This is generally not allowed in practical applications (except for controlled membrane mechanical seals).
Most of the working conditions between the dynamic and static rings of mechanical seals are in the state of boundary lubrication and semi liquid lubrication. Semi liquid lubrication can achieve the best sealing effect with the minimum friction coefficient, that is, satisfactory wear and heat.
In order to make the mechanical seal work under good lubrication conditions, it is also necessary to comprehensively consider the factors such as medium characteristics, pressure, temperature, sliding speed, etc., but the selection of appropriate pressure between dynamic and static rings, reasonable lubrication structure, and improvement of the friction surface quality of dynamic and static rings are also important factors to ensure the effective work of the seal.