204 Mechanical seal What is the connection with evacuation?
According to the statistics of China's petrochemical industry, more than 80% of centrifugal pumps use mechanical seals. Due to the different working conditions of the mechanical seals of centrifugal pumps, material leakage often occurs in the process of conveying materials, polluting the environment and wasting energy.
Mechanical seal is one of the main wearing parts of centrifugal pump, and pump failure is mainly caused by seal failure. According to statistics, the failure of mechanical seal leads to pump failure accounting for more than 50% of equipment failure rate. Therefore, it is necessary to analyze and improve the leakage of mechanical seal of centrifugal pump to reduce the pump failure rate.
1、 Working Principle of Centrifugal Pump and Function of Mechanical Seal Device
The centrifugal pump makes its impeller rotate at high speed through the motor and coupling. The liquid between the blades is pushed by the blades. Under the centrifugal force, it is constantly thrown from the center to the periphery. When the liquid in the pump is thrown from the center of the impeller to the edge, a low-pressure area is formed in the center. Since the liquid pressure before entering the pump is greater than the pressure at the pump suction, under the effect of the pressure difference, The liquid will be continuously sucked into the pump through the suction pipe to supplement the position of the discharged liquid. As long as the impeller keeps rotating, the liquid will be continuously sucked in and discharged.
When the pump shaft passes through the pump housing, if there is a gap between the dynamic and static parts, the liquid in the pump will leak out of the gap. If the suction end is vacuum, the external air will leak into the pump, which will seriously affect the operation of the pump. In order to reduce leakage, the shaft end sealing device is generally installed at the dynamic and static gap. The shaft seal device is an important part of the centrifugal pump, which is directly related to whether the centrifugal pump can work normally. Now the shaft seal device generally adopts mechanical seal.
2、 Mechanical seal principle
Mechanical seal is an axial end face sealing device that relies on the elastic element to preload the moving and stationary ring end face sealing pairs and the medium pressure and the elastic element pressure to achieve sealing.
Mechanical seal usually consists of static ring, dynamic ring, compression element and sealing element. The end faces of the moving ring and the stationary ring form a pair of friction pairs. The moving ring presses its end face against the end face of the stationary ring by the pressure of the liquid in the seal chamber, and produces appropriate specific pressure on the end faces of the two rings and maintains an extremely thin liquid film to achieve the purpose of sealing.
The pressure generated by the pressing element can make the pump keep the end face close when it is not running, ensure that the sealing medium does not leak out, and prevent impurities from entering the sealing end face. The seal ring plays a role in sealing the clearance between the moving ring and the shaft, the clearance between the stationary ring and the gland, and also plays a buffer role in the vibration and impact of the pump. The mechanical seal is not an isolated part in actual operation, it is combined with other parts of the pump to operate.
3、 Auxiliary facilities of mechanical seal - flushing device
The flushing device is the main auxiliary facility of the mechanical seal. During the operation of the pump, impurities are deposited or formed in the seal chamber, which must be flushed. Otherwise, the dynamic and static rings of the mechanical seal will lose their floatability and the spring will fail due to the precipitation of crystals and particles. More serious is the particle wear, impurities into the friction pair will intensify the wear, leading to rapid failure of mechanical seals. Therefore, in general, the mechanical seal for pump shall be flushed.
There are many flushing schemes for mechanical seals (as shown in the figure below), which are suitable for different working occasions. The next issue will introduce them in detail.
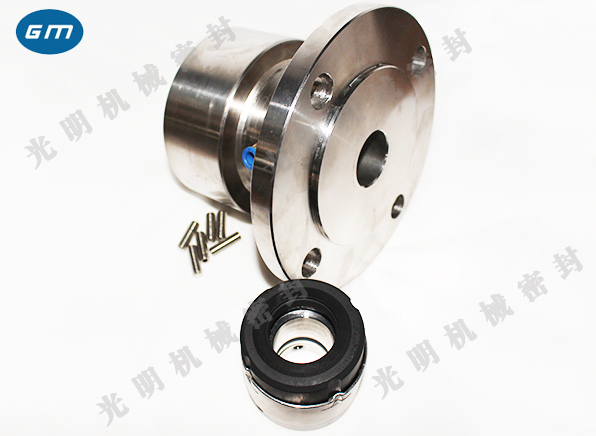
4、 Cause analysis of mechanical seal leakage
When the newly installed (or replaced) mechanical seal is put into operation, the leakage shall be within the allowable range. If there are no problems in the structure, manufacturing quality, installation and use of the seal itself, its service life will exceed 8000h. In actual work, many seals fail far before their service life reaches this value, which is caused by certain problems in process conditions, equipment operation and operation. According to the operating conditions of mechanical seals and the disassembly and inspection after failure in recent years, the common reasons are as follows:
1. Hot crack of sealing ring
When the mechanical seal is disassembled, it can be found that the surface of the hard ring has overheated tempering color, the surface of the graphite ring has annular grooves, and the rubber ring is aging.
The main reasons are as follows: ① Cavitation is formed in the pump body due to high medium temperature. After cavitation occurs, the hydraulic impact drives the seal to make rapid axial oscillation, which causes serious wear of dynamic and static rings, auxiliary seal rings and other parts, and damages the mechanical seal device. ② Poor lubrication, no liquid lubrication film is formed on the end face of the seal ring, or the liquid film between the end faces of the seal ring vaporizes, resulting in dry friction; ③ Poor heat dissipation of cooling system;
2. Vibration of centrifugal pump
Due to manufacturing and installation accuracy, all centrifugal pumps are subject to vibration. The main causes of vibration are rotor imbalance, pump misalignment, rolling bearing failure, etc. The maximum amplitude measured from the surface of the bearing box shall not be greater than 0.06mm. If it exceeds this value, the pump shall be stopped for treatment. The vibration can be divided into three directions: vertical, horizontal and axial. The axial vibration is the most harmful to the seal. When the pump vibration intensifies, the dynamic and static rings are separated. The instantaneous separation causes the sealing surface to open under the pressure of the liquid film, and a large amount of leakage occurs. If the solid particle content in the medium exceeds 5% at this time, the vibration causes the end face to separate, and the particles are embedded in the soft end face of the graphite ring, causing excessive wear of the hard ring sealing surface. It can be found during disassembly inspection that there are clear friction marks on the hard sealing surface and scratches when entering solid particles.
3. Elastic element loses elasticity
The main feature is that when the elastic element is disassembled for inspection, the elastic element has insufficient elasticity, deformation and obvious reduction of free height. The probability of this situation is relatively small
The main reasons are as follows: ① Most of the materials used to make springs and bellows will have the defect of decreasing elasticity when they work at high temperature for a long time, so that the closing force of the seal face is insufficient, resulting in serious leakage of the seal face. The high temperature elastic loss of metal bellows is a common and typical failure form of such mechanical seals; ② Creep, fatigue failure, etc. of spring during long-term operation under high temperature; ③ The spring has been corroded and failed under high temperature for a long time.
5、 Epilogue
When the centrifugal pump is working below the minimum flow value, the fluid in the pump has serious backflow and other phenomena, resulting in temperature rise and vibration.
Evacuation is one of the many reasons for the failure of centrifugal pump, which will be accompanied by the following conditions:
① . Motor current drops
② Pressure fluctuates greatly
③ Abnormal fluctuation of flow
④ , making noise
⑤ The pump body vibrates
⑥ Pump cylinder temperature rises