1. What is the face specific pressure of mechanical seal?
The remaining closing force per unit area on the seal ring is called end face specific pressure, expressed in Pa. Whether the end face specific pressure in MPa is appropriate has a great impact on the performance and service life of mechanical seals. If the specific pressure is too high, it will intensify the wear of the seal face, destroy the fluid film, and reduce the service life; Too small specific pressure will increase seal leakage and reduce sealing performance.
2. How is the mechanical seal stressed?
The analysis of the force on the seal is to analyze the type and size of the force on the seal ring in the working state, and then calculate the face specific pressure of the mechanical seal. The stress of the seal is related to the design structure of the seal. Figure 3-1
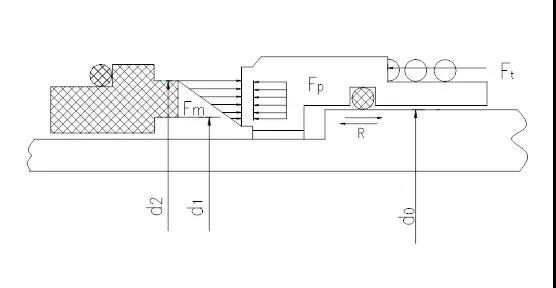
Figure 3-1 Stress Analysis Diagram
The forces acting on the moving ring include the spring Ft medium force Fp and the fluid film pressure Fm, in addition to the friction resistance R of the seal ring, where the direction of the medium force and the spring force is the same, which is called the closing force. The liquid film pressure Fm is the pushing force, and the actual force of the friction resistance R is very small and can be ignored, so the resultant force of the seal is F=Ft+Fp - Fm.
3. How many methods are there to test the spring force?
There are generally two methods to test the spring force. The spring force is the main factor of the sealing closing force. This force can be obtained by calculation method but has certain errors. In fact, it is more accurate to measure it by actual measurement. In the field, the measurement method is to add weight to the spring and record the compression height. The spring force can also be measured. The other is to use the spring testing machine to measure. The spring testing machine has two kinds of methods: mechanical pointer display method and electronic digital display method. At present, these two methods are basically used and their testing methods are relatively accurate.
4. What is the spring specific pressure? How to calculate?
The spring specific pressure is the spring force on the unit sealing surface, in MPa. The calculation method is to divide the total spring force by the area of the sealing section. Generally, the specific spring pressure of built-in mechanical seal is 0.1~0.2 MPa. For external mechanical seal, when the medium force is less than 0.1 MPa, the spring specific pressure is 0.3~04 MPa, and when the medium pressure is less than 0.25, the spring specific pressure is 0.4~06 MPa.
5. How is the load factor defined? What is the meaning?
The ratio of the effective area of the closing force of the sealing medium pressure acting on the compensation ring (moving ring) against the non compensation ring (stationary ring) to the area of the sealing ring is called the load coefficient. For example, for a built-in mechanical seal, let the effective area Ae of the sealing medium and the area A of the sealing ring belt, so the load coefficient can be obtained from Figure 3-2

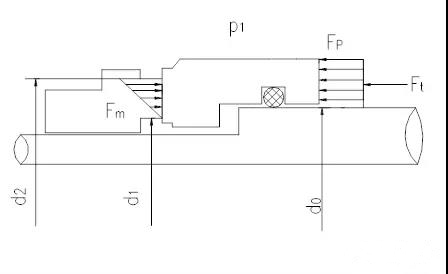
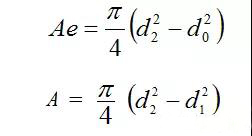
Bring the sum value into the
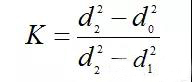
K is the load factor for fluid mechanical seals. Different sealing structures can be calculated according to the definition of load factor. The load factor is of great significance. It is an important parameter used to distinguish balanced and unbalanced seals. It has a great impact on the leakage and service life.
6. How are balanced and unbalanced seals selected?
For ordinary medium, when P medium=0.6~0.7Mpa or above, balanced seal is selected. For medium with high viscosity and good lubrication performance, the use pressure of unbalanced mechanical seal can exceed this value; For medium with low viscosity and poor lubrication performance, when P medium=0.29~0.49Mpa, balanced mechanical seal must be selected.
The balanced mechanical seal is used to reduce the pressure of the sealing medium on the end face, so that the specific pressure of the end face is within the appropriate range.
When the pressure of the seal chamber exceeds 0.7 mpa, partial balance type seal shall be adopted.
7. How are balanced and unbalanced mechanical seals divided?
According to the unloading of the specific pressure caused by the end face of the medium, seals can be divided into two types: balanced and unbalanced. Non unloading is called unbalanced type; Unloading is called balanced type. Figure 3-3 is unbalanced type. Figure 3-4 is balanced type
Fig. 3-3 Unbalanced seal 3-4 is balanced
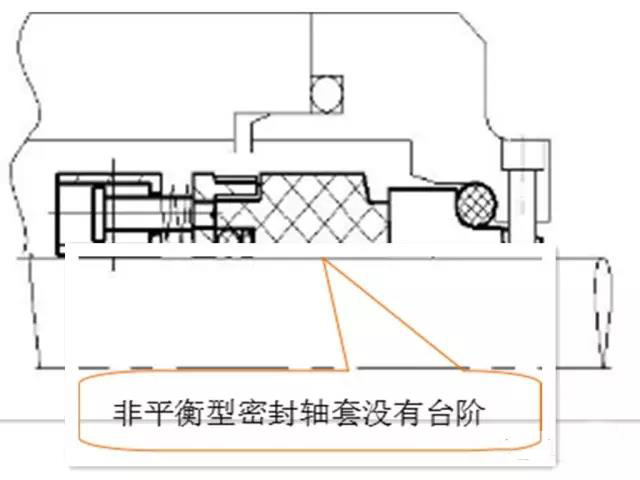
Non equilibrium type - the end pressure is affected by the medium pressure. Excessive pressure will damage the lubricating film of end clearance.
Balanced type - the pressure of the sealing surface of the dynamic and static rings is not (or is rarely) affected by the medium pressure
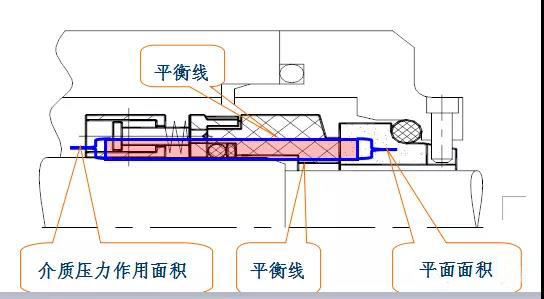
The sealing ring area of balanced seal is larger than the area of fluid pressure action. For this reason, the outer diameter of the seal face is higher than the balance line and the inner diameter is lower than the balance line. This requires a step on the shaft or shaft sleeve. On the contrary, the non-equilibrium seal ring belt is less than the area under the action of fluid pressure, and the non-equilibrium seal can be directly matched with the optical shaft. The balance line is shown in Figure 3-5
The seal with load factor K ≥ 1.0 is a non-equilibrium seal.
The seal with load factor K < 1.0 is called balanced seal.
K load coefficient of centrifugal pump in general petrochemical industry is K=0.63~0.85
When the pressure of the sealing chamber exceeds 0.7 mpa, the partial balance type shall be adopted
8. How to determine the balance coefficient?
The balanced type is mainly used to reduce the force exerted on the end face by the sealed medium, so that the end face specific pressure can be used within the appropriate range.
The selection of balance coefficient ß is related to the viscosity, temperature, speed of sealing medium, etc.
The common range of ß value is 15%~40%, that is, the load coefficient K=0.85~0.60. Under the condition that other conditions do not change, the larger the viscosity, the smaller the applicable ß value, and the smaller the viscosity, the larger the applied ß value. The test proves that the ß value of water, gasoline, kerosene and other media is about 20%~30% (when the ß value of water=48, it is close to the limit of end face opening; when the ß value of oil with high viscosity is about 30%~40%, the ß value of mechanical seal is divided into 15%, 20%, 25%, 30% and 40%.
9. What effect does the balance coefficient ß value have on the seal?
The larger the balance coefficient ß, the smaller the end face specific pressure caused by the medium. Although the wear is small, it is not easy to ensure the sealing. On the contrary, the smaller the balance coefficient ß is, the greater the specific pressure of the end face will be, which will aggravate the wear of the end face, heat and even the risk of biting, and finally make the seal invalid. Therefore, appropriate ß value should be selected. The value is related to many factors, and the situation is complex. Generally, ß value is not easy to exceed 0.5, otherwise, the counter pressure between the end faces will push the end faces away.
10. How to calculate the face specific pressure of commonly used built-in mechanical seals?
The face specific pressure of mechanical seal is an important factor to ensure the long-term operation of mechanical seal. The specific pressure of the end face shall be greater than the liquid film pressure of the sealing end face, so as to make the seal fit well and ensure the stability of the seal. However, the specific pressure of the end face should not be too high to prevent a large number of heat damage to the liquid film of the seal, or even cause wear and thermal cracking of the seal end face.
The calculation of end face specific pressure is related to the design structure of the seal. Different structures have different calculation methods. It should be pointed out that the end face specific pressure is the average value of the load per unit area,
Figure 3-2 is the schematic diagram of the built-in balanced mechanical seal mechanism. It is a widely used form. According to question and answer 55
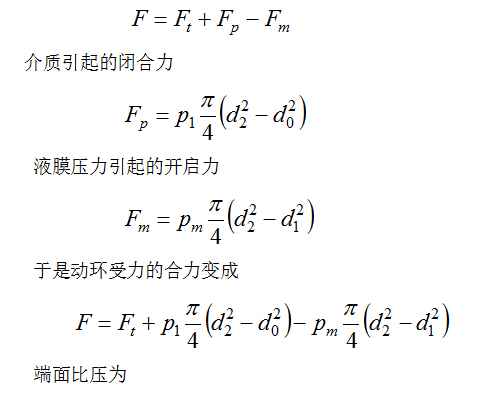
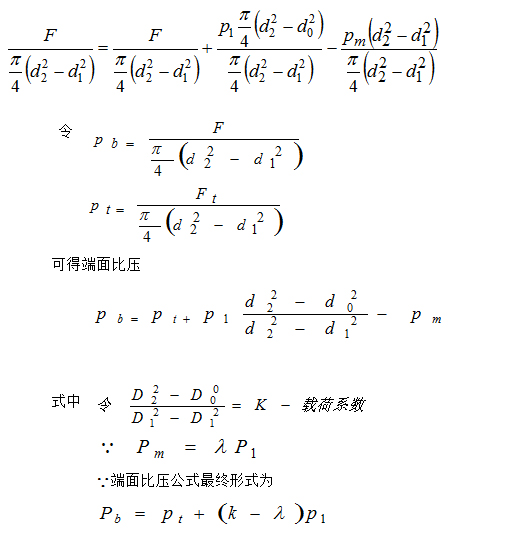
This is the end face specific pressure calculation formula of the internal flow rotating mechanical seal. This formula is applicable to the same non-equilibrium seal.
Examples; There is a centrifugal pump with built-in mechanical seal: relevant dimensions of mechanical seal are: d0=60mm, D1=62mm, D2=70mm, Spring force under known design conditions P spring=150 N: solid side sealing cavity medium pressure P=0.3Mpa; Find the end face specific pressure of the pump?
Solution; Use formula
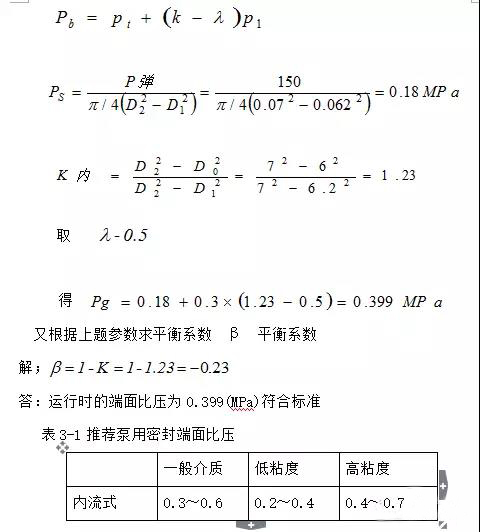
11. How to calculate the specific pressure of bellows seal face?
For bellows seals, the calculation of face specific pressure is exactly the same as that of spring seals, except that when calculating the balance coefficient, the effective diameter of bellows is used instead of the average diameter of spring seals. The effective diameter of the bellows is related to the working state, waveform, wave number and material of the bellows. The sealing of welded bellows can be calculated according to the following formula.
Where - is the inner diameter of bellows
- is the outer diameter of the bellows
- Effective diameter of bellows
The calculated value of the above calculation formula has a certain deviation from the actual value. The greater the pressure, the greater the deviation.
12. What is the commonly used end face pressure value?
The commonly used face specific pressure value is the main technical parameter to ensure the normal operation of the seal. The face specific pressure value is related to the structure, medium pressure, working conditions, etc. of the mechanical seal. Table 3-1
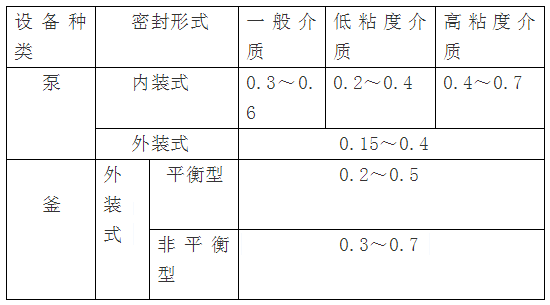
13. What is the pv value of mechanical seal?
The friction power of the seal face depends on the pressure and speed. Therefore, the product of the two is often used in engineering, that is, the pv value. Pv is often used as an important parameter for seal selection. If the pv of the mechanical seal is too large, a large amount of friction heat will be generated on the sealing surface, which may cause the seal liquid film to vaporize and seal leakage. The serious one causes serious wear and tear of the sealing end face, which results in grooves and cracks. Therefore, pv is an important parameter for normal operation of the seal, and pv of mechanical seal refers to the product of face specific pressure and circumferential velocity.