External causes affecting the mechanical seal for pump Mechanical seal for kettle The manufacturer tells you!
(1) Axial displacement of pump shaft
The sealing surface of mechanical seal shall have a certain specific pressure (0.4~0.6MPa) to achieve the purpose of sealing. The tightness of both ends can be adjusted by spring. In order to ensure this specific pressure, the pump shaft is required not to have too much displacement (≤ 0.5mm), but in actual production, the pump shaft often has a large displacement.
It is very unfavorable for the use of mechanical seal. This situation is manifested in the process of pump startup in our branch factory. Due to the existence of unbalanced axial force, the entire shaft moves towards the suction port, causing the mechanical seal to lose its sealing effect. Common measures include: opening balance holes on the impeller, installing balance pipes on the pump body, etc.
(2) The deflection of pump shaft is too large
When the shaft is bent and deformed, the linear displacement of the cross section centroid in the direction perpendicular to the axis is called deflection. Mechanical seals require uniform force between the two seal faces. However, due to the unreasonable design of the pump product, the deflection at the mechanical seal installation is too large, which makes the force on the seal uneven, thus losing the sealing effect. This phenomenon mostly exists in horizontal multistage centrifugal pumps.
(3) No auxiliary flushing system or unreasonable design of auxiliary flushing system
The auxiliary flushing system of mechanical seal is very important. It can effectively protect the sealing surface and play the role of cooling, lubrication and flushing away debris. Sometimes the designer's design is unreasonable, and the sealing effect cannot be achieved; Some have designed auxiliary systems, but because of impurities in the flushing fluid, insufficient flow and pressure of the flushing fluid, unreasonable design of the flushing port position and other reasons, the effect is also not achieved. Common measures include:
1. If conditions permit, try to design auxiliary flushing system. The flushing pressure is generally required to be 0.107~0.11MPa higher than the pressure of the seal chamber. The pressure of the seal chamber shall be calculated according to the structure of each pump, system pressure and other factors. When the pressure of the shaft seal cavity is very high or close to the highest limit of the seal, the seal cavity can also lead the liquid to the low-pressure area to make the shaft seal liquid flow to take away the friction heat.
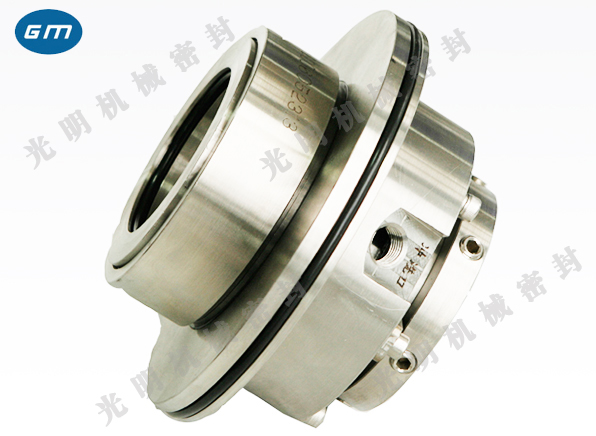
2. Reasonably configure pipelines and accessories according to the operating conditions of each pump. Such as cooler, orifice plate, filter, valve, flow indicator, pressure gauge, temperature, etc. In fact, the reliability and life of the seal largely depend on the configuration of the auxiliary seal system. In addition, the existence of reasons such as insufficient machining accuracy of the pump shaft, shaft sleeve, pump body and seal cavity is also very unfavorable to the sealing effect of the mechanical seal, and strict checks should be made in these aspects.
(4) Excessive vibration and elimination measures
The excessive vibration of the mechanical seal is often not the reason of the mechanical seal itself, but the unreasonable design of the pump shaft, insufficient machining accuracy, excessive parallelism of the coupling, large radial force and other reasons. The measures to eliminate the pump vibration include: when the auxiliary equipment such as the pump, motor, base, and on-site pipeline are installed on the site, strict control should be taken to eliminate the vibration source.
(5) Causes of pump cavitation and improvement measures
The inlet of the impeller of the centrifugal pump is the place with the lowest pressure in the pump. When the pressure here is equal to or lower than the saturated vapor pressure of the conveyed liquid 1pt at the operating temperature, the liquid will boil and vaporize, producing a large number of bubbles. At the same time, the bubbles dissolved in the liquid will also be separated. These vapors flow with the liquid to the higher pressure in the impeller, where the bubbles condense again.
During the condensation process, due to the sharp reduction of the volume, the surrounding liquid rushes into the entire condensation space at a great speed, causing shock vibration and noise in the pump. Under the continuous impact of liquid particles with high pressure and frequency, the metal surface is gradually damaged due to fatigue, which is called denudation.
At the same time, oxygen and other active gases dissolved in liquid also cause corrosion of metal. Due to the combined effect of chemical corrosion and mechanical denudation, the metal damage speed is accelerated, thus the impeller is damaged, which is called cavitation damage. This impact phenomenon caused by the vaporization and condensation of liquid is called cavitation. The measures to eliminate cavitation at pump inlet are as follows:
1. Improve the cavitation performance of the pump to meet the requirements of cavitation performance of field devices.
2. The pump shall be operated below the allowable suction height to ensure the safe and reliable operation of the whole device.
3. Impellers made of cavitation resistant materials, such as 2Cr13, rare earth alloy cast iron, high nickel chromium alloy materials, are much better than ordinary cast iron in terms of cavitation resistance.