With the development of modern petroleum, chemical industry, metallurgy, atomic energy, electronics and aerospace technology, the sealing requirements for high-pressure, ultrahigh pressure, high vacuum, ultrahigh vacuum and even ultrahigh vacuum equipment for different purposes are becoming higher and higher. Some of them have complex structures, with many pipes and transmission mechanisms inside; Some are very large, hundreds of cubic meters, or even thousands of cubic meters. In these equipment, the total length of pipelines can reach several kilometers, and the total length of welds and seal connections can reach tens of kilometers. The workload of leak detection is huge. In fact, it is difficult to manufacture a leak free device, and it is impossible to achieve leak free in a sense. Therefore, in general, leak detection tests should be carried out on the manufactured equipment. No matter which leak detection method is used, it will always take a certain amount of time, manpower, material resources and financial resources. Therefore, when conducting leak detection test, it is necessary to correctly understand and use the leak detection method, minimize "missed diagnosis and misdiagnosis", and try to carefully consider the sealing problem from the stages of preparation, design, processing, installation, commissioning, formal operation, etc. of the project or the complete set of devices, Take various effective measures to reduce leakage. The following describes the leakage prediction, prevention and leak detection procedures during the design, manufacturing, installation, commissioning and operation of the device.
Project preparation stage
1、 Main issues to be considered during project preparation
In the stage of device manufacturing, purchase and inspection, full attention must be paid to the sealing problem, especially in the project preparation stage, that is, when considering what kind of devices can be manufactured and purchased to meet the use requirements, more attention should be paid. Site conditions, economy, performance, safety and environmental issues of the device should be considered in the preparatory stage. In fact, at this stage, the main factors that may cause leakage and what measures should be taken in case of leakage should be carefully considered, mainly including:
1. Understand the process principle and method of the device, that is, which part of the process flow the device manufactured is installed in, what role it plays, and how to use it;
2. Understand the working conditions of equipment and devices, including the temperature, pressure, medium characteristics used, and possible impact, vibration, and fluctuations in process conditions;
3. Determine the allowable leakage rate, that is, the specified indicator leakage rate, and specify how to detect and repair the leakage when it occurs;
4. How to ensure the durability of the device, that is, to ensure that the leakage rate of the device will not increase under normal operating conditions; Formulate measures to be taken in case of abnormal conditions during use;
5. Analyze the danger of the device and possible emergencies, predict whether the device can withstand emergencies when operating incorrectly, as well as the degree of danger and scope of influence when emergencies occur;
6. Formulate clear and effective standards and corresponding measures, and judge the required funds and possible effects.
2、 Indicator leakage rate
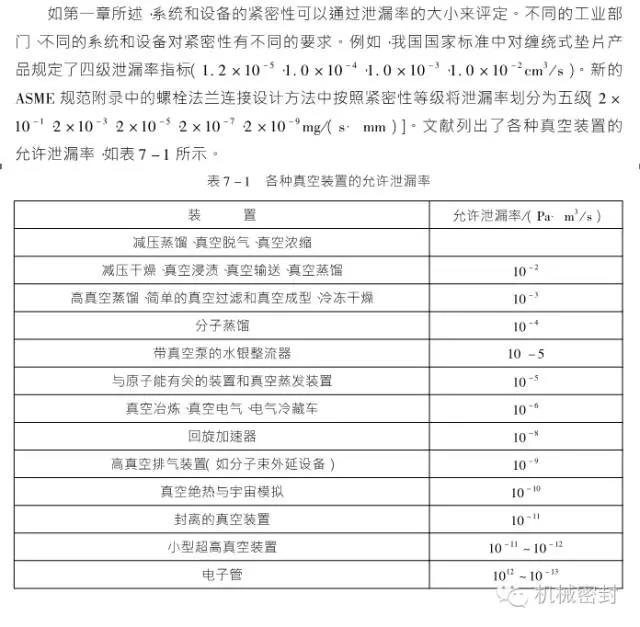
It can be seen that no matter what the situation, it is difficult to specify the allowable leakage rate in general. Even if the devices are the same, due to the design The working conditions of manufacturing and use vary greatly, and the allowable leakage rate will change with the change of one condition. If the cost is not considered, the stricter the requirements on the allowable leakage rate, the more conducive to safety.
As shown in Table 7-1, when determining the allowable leakage rate of the pressure device, various complex factors should be taken into account, among which the most difficult one is To estimate the pollution of leaked gas and liquid to the surrounding environment, or the resulting danger
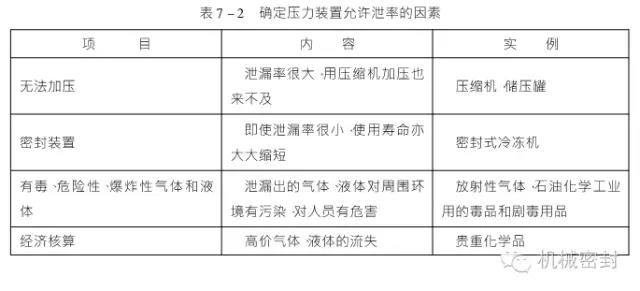
The leaked gas or liquid diffuses around after gasification, due to the diffusion coefficient, nature, temperature, wind speed and wind speed of the gas The diffusion speed and diffusion state vary greatly due to different directions, topography and other conditions, so even if the leakage rate is the same, the risk to the environment and personnel will be different.
3、 Relationship between the leakage condition and the running time of the device
With the increase of service time, the performance of any device will continue to decline. Leakage rate of common devices It will increase with the increase of service time. As shown in Figure 7-1, during the continuous use of the device, the leakage rate will also continue to increase, until a certain moment, the leakage rate suddenly exceeds the allowable leakage rate, causing serious leakage, resulting in the device being unable to operate, even environmental pollution or serious loss of personnel and property. Therefore, in each stage of planning, design, manufacturing, purchase, assembly and construction, the goal should be to meet the allowable leakage rate, and the tightness of the device should be maintained as long as possible. But in fact, this requirement is difficult to achieve, so it can only be remedied through regular maintenance and routine maintenance. Any department shall establish the maintenance standard and regular maintenance plan of the device.
In fact, in many enterprises' device maintenance plans, leakage is often not clearly defined, and some even I didn't think about it seriously in the equipment stage of the project.
The increase of leakage rate during the operation of the device, the occurrence of sudden leakage accidents and their prevention and solution measures should be carefully considered, which is not only necessary to prevent the occurrence of hazards and accidents, but also important to understand the reliability and durability of devices and components. In addition, important technical data can be obtained by comparing the actual operation state and the ideal state of the device, which is of great significance to the design, manufacture and maintenance of the device.
The strict leak detection test and the improvement of the allowable leakage rate index are to improve the reliability of the device and extend the maintenance cycle of the device Important guarantee of. However, even though strict leak detection tests have been carried out, the occurrence of leakage must be noticed frequently during use. If possible, the probability of leakage and the measures that should be taken should be understood, the standards for routine and regular maintenance should be improved, and the interval between regular maintenance should be determined.
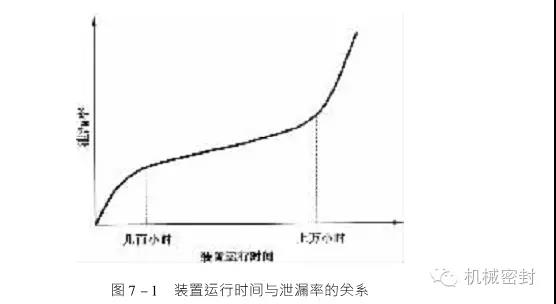
design phase
There are many stages from basic design to actual design including each part drawing and assembly drawing Leakage should not be ignored at any stage. Although there are various reasons for leakage at the equipment manufacturing stage and the inspection stage, experience shows that most leakage problems occur at the design stage. Therefore, if attention can be paid at the design stage, it is possible to greatly reduce the occurrence of leakage and the resulting accidents. In the design phase, the following items should be considered for leakage.
(1 )Reasonably specify the maximum allowable leakage rate of equipment, and then specify the maximum allowable leakage rate of all parts and components.
(2) What kind of leak detection instrument and leak detection are used for different parts (or the whole equipment) during processing, installation and operation method.
If pressure leak detection method is used, consider:
1. Pressure resistance of the container after inflation;
2. Whether there are materials in the container that will be corroded by the leakage gas;
3. Whether the weld position is exposed during leak detection;
4. How to inject leak indicating gas;
5. If ammonia, radioactive gas, etc. are used in the leak detection process, the devices such as discharge, flushing and recovery shall be considered in the design.
If vacuum leak detection method is used, consider:
1. Whether the container is allowed to be in negative pressure state;
2. What kind of vacuum pump is used;
3. Connection method of leak detector.
(1) The process design shall be reasonable. For example, usually only one side of the vacuum container is allowed to have welds. If it is necessary to increase the strength of the welds The vacuum side shall be welded continuously, and the non vacuum side shall be welded intermittently.
(2 )Leakage should also be considered when selecting materials. When selecting metal materials, the tensile strength, compressive strength, high temperature strength, low temperature brittleness, hardening characteristics, machinability, weldability, corrosion resistance during use, etc. shall be considered. The selection of organic materials is usually much more difficult than that of metal materials. Organic materials shall be selected according to the purpose of use, temperature, pressure, mechanical properties (compression rate, rebound rate, resilience), durability, etc. Factors related to leakage, such as material compactness, air permeability, surface vapor pressure, etc., shall be fully considered in the selection process.
(3) The requirements for sealing, leakage detection and repair shall be fully considered during structural design. Avoid "sending" as much as possible in the design To shorten the response time of leak detection. Precautions for structural design are shown in Table 7-3.
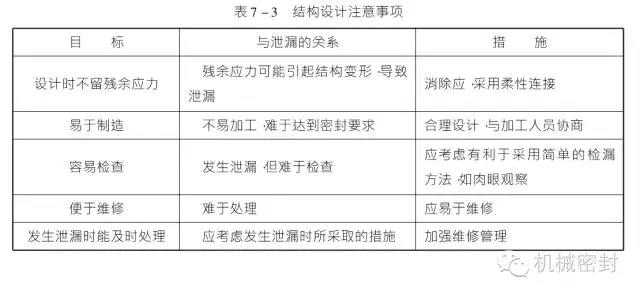
Processing and manufacturing stage
Leakage during processing and manufacturing is usually related to the manufacturing level and the quality of processing personnel, such as electric welders Low level, or not processed according to the drawing requirements. Sometimes, the consequences caused by poor consideration of sealing problems during design can be remedied through processing and manufacturing. Therefore, it is very important for processing and manufacturing personnel to have the basic knowledge of sealing and always pay attention to leakage.
In the process of processing and manufacturing, leakage shall be mainly considered as follows.
1、 Leakage detection of weldments
Whether the welds of equipment parts need leak detection shall be based on the welding quality and the maximum leakage rate allowed by the equipment To determine. The leakage detection of welds shall be carried out during the processing of parts or after the general assembly, depending on the specific situation. For example, since the weld of some equipment is not exposed after assembly, repair welding cannot be carried out even if a leak is found. For another example, the volume of some large containers is too large after final assembly, so the leak detection sensitivity may be very low, and small leaks cannot be detected, thus failing to meet the requirements of leak detection. For vessels and equipment like this, leakage detection shall be carried out on the welds during the processing of parts.
The parts that have been leak checked shall be leak checked again after cutting the weld, and the weld after repair welding shall also be re welded New leak detection.
II Leakage detection of other machined parts
The metal plate generally does not need leak detection (except for castings), but the metal plate with surface and internal defects (slag inclusion, porosity, cracks) If it is a material, leak detection must be carried out.
The machined workpiece generally does not need leak detection. However, the thin-walled pipe may have cracks after bending, so it is necessary to conduct leak detection on the bending part.
3、 Machining
Compared with welding, machining generally does not cause leakage. When machining, the size and precision shall conform to the drawing It is OK to ask for it, and there is usually no need to take additional measures.
When machining the casting parts, the casting pores may be exposed after removing the oxide skin on the surface. Although cast Blowhole may not always cause leakage, but for devices and components with strict leakage rate requirements, such castings shall be scrapped or effective repair measures shall be taken. The smoothness of the sealing surface has a significant impact on the sealing performance of the connection. For metal seals, the higher the smoothness of the sealing surface, the better the sealing effect. For non-metallic gaskets, it is not necessary to use high finish. In addition to the sealing effect of the connection, the machining cost should also be considered when selecting the sealing surface finish. In addition, the sealing surface of the connection must be protected to avoid scratches and other defects during processing, assembly and use.
4、 Assembly process
It is very important to pay attention to leakage during assembly. In the assembly stage, the problems in the previous stages can be solved Conduct comprehensive inspection, and further inspect the leakage prevention measures taken in the design or processing stage. During the assembly process, the dimensional accuracy, surface processing status, and whether there are scars of each component can be checked again. According to the assembly condition, it can also be roughly judged whether the equipment will leak. The experience and technical level of the assembly personnel will have a great impact on the quality of the assembled equipment.
Installation and commissioning stage
In previous stages, the leakage problem has been carefully noticed, and the leakage test has been carried out, but whether it is really effective It still needs to make a comprehensive judgment in the installation and commissioning stage.
Leakage detection problems to be considered during installation and commissioning are as follows:
1. If parts and components subject to leakage detection are subject to greater mechanical shock or vibration, leakage detection shall be conducted again before final assembly.
2. Leak detection shall be carried out step by step according to the installation sequence. It is better to check the leakage of this component and the connection after each component is installed, and install the next component after the leakage is qualified.
3. During installation, some parts that have been reprocessed shall be re leak checked. For example, some pipes bear heavy loads during assembly or are re bent, which will cause cracking of welds and base materials. At this time, leakage detection must be carried out again.
4. After installation, leak detection shall be carried out at the sealing joints first, and then sectional and overall leak detection tests shall be carried out.
5. Generally, pressure drop method or static pressure rise method can be used for overall leakage test. If the leakage rate allowed by the system is low, the test time shall be appropriately extended. Use a calibrated pressure gauge, vacuum gauge or transmitter. Since the detection elements are usually affected by the changes of air temperature and pressure, they should be corrected if necessary. If the total leakage rate of the system is lower than the allowable leakage rate, the test can be ended and the operation phase can be started. On the contrary, if the total leakage rate of the system is higher than the allowable leakage rate, further leakage detection shall be carried out to find out the causes and points of leakage, and repair, replacement and other measures shall be taken.
6. Before the overall leak test, it is better to conduct sectional leak detection first. During the test, close the valves connecting various devices or temporarily install blind plates to divide the whole device into several sections. Then, each section shall be leak checked. Pressure drop method or static pressure rise method can also be used for leak detection. In order to shorten the test time, leakage detection of each section can be carried out at the same time. If necessary, other detection instruments and methods shall be used for leakage detection to determine the leakage condition of each section and find out the leakage point. For parts to be baked or cooled, leakage detection must be conducted after cold and heat shock tests. For example, for cold trap, cooling baffle and other parts, after baking and degassing, coolant (liquid nitrogen, Freon, etc.) shall be injected immediately, and then the leakage rate shall be measured. It is worth noting that in these processes, leakage does not necessarily occur in the coldest or hottest state.
7. If leakage is detected and the leakage point is determined, repair or replace it immediately. The repaired or replaced parts or equipment shall be retested until they are qualified. Table 7-4 lists some causes of leakage and measures to be taken.
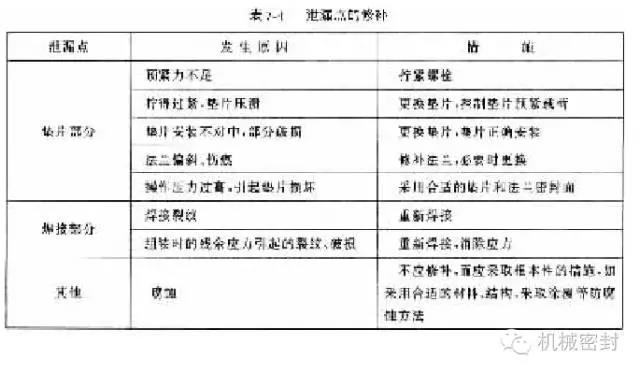
Operation and maintenance phase
If thorough leak detection and repair have been carried out in previous stages, there will be no leakage in a short time. In the formal operation stage, if leakage often occurs, the review in the planning, design and processing stages shall be conducted again according to the different nature of the leakage. In the operation and maintenance phase, the following work should be done well.
1、 Operation journal
In order to continuously revise the maintenance plan prepared in advance and make it more perfect, detailed records should be made Spare every Days of operation. Leakage shall also be recorded in the equipment operation diary. Record not only the changes of system pressure, temperature and flow, but also the conditions related to leakage. Because the leakage is related to many factors such as working conditions, media, equipment structure, materials, etc., it is sometimes difficult to find out the cause of the leakage. If there are detailed records, it is convenient to make correct judgments based on the records and take corresponding preventive measures. In addition, the maintenance and inspection contents shall also be recorded in detail.
2、 Maintenance and inspection
In the operation and maintenance of equipment, great attention should be paid to the leakage problem and corresponding measures should be taken. For example, actively advance The leak detection test is also part of the maintenance work. For the pressurizing device, a leak detector can be used for patrol inspection once a day; For the vacuum device, the valve of the exhaust system can be temporarily closed, and the static pressure boosting method can be used for a short time leak detection test. After some parts are replaced, if there is a leakage fault, the specific leakage point can often be determined after comparing with the condition before replacement. If the operation of the equipment can be recorded every day, in addition to sudden leakage, it can generally predict when the system will have a leakage problem exceeding the allowable leakage rate. During actual use, the maintenance plan should be gradually modified to make it more consistent with the actual situation.
3、 Regular maintenance
Regular maintenance is very important to prevent leakage. In case of leakage at ordinary times, the equipment cannot be stopped, and only temporary measures can be taken Sexual measures. During regular maintenance, because the equipment stops running, it can be completely repaired or replaced with new parts, and the replaced parts should be leak checked. In addition, regular maintenance can further find out the causes of leakage and find out the methods to prevent leakage accidents.
(The images and texts of this platform are reprinted from the network, and the purpose of reprinting is to convey more information. We respect the original, and the copyright belongs to the original author. If we cannot find the author and source, we hope to understand, thank you.)