Discussion on Common Damage Causes and Maintenance of Dry Gas Seal
The sealing weir prevents the gas from flowing to the middle, so that the gas is compressed, causing a pressure rise, and the seal end clearance is statically determined to form the required gas film. The balance clearance (film thickness) of seal face is generally 2~10 μ M. In this way, the clearance of the end face can control the opening force of the interface by itself, balance with the external closing force, make the gas film have good elasticity (high gas film stiffness), form a stable operation and prevent the sealing end faces from contacting each other.
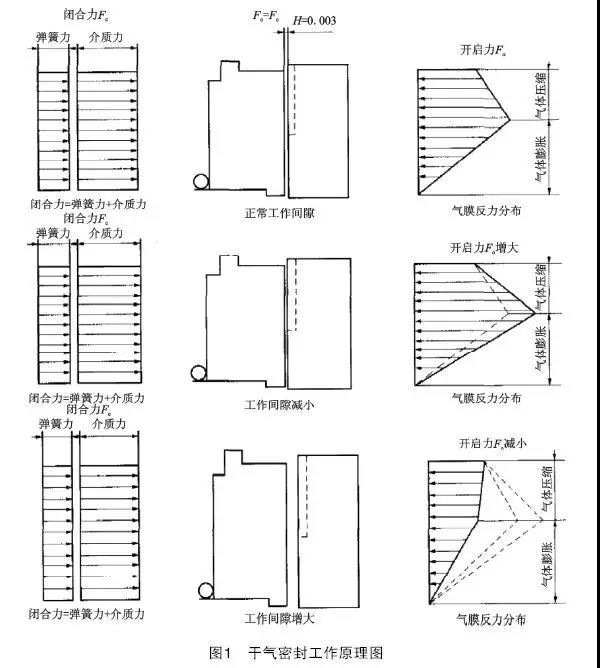

The structural form of dry gas seal can also be divided into single end dry gas seal and double end dry gas seal (see Figure 3) according to the different sealed media, media pressure and working speed (see Figure 3), which is applicable to the harmless working conditions when a small amount of process gas leaks into the atmosphere, such as carbon dioxide machine, air compressor, nitrogen compressor, etc; The double end face arrangement (see Figure 4) is applicable to the condition that the process gas is not allowed to leak into the atmosphere, but nitrogen is allowed to enter the unit, for example, the process gas is dirty, unstable or there is a risk of negative pressure; The tandem arrangement (see Figure 5) is applicable to the condition that a small amount of process gas is allowed to leak to the atmosphere. The two-stage tandem arrangement is adopted, one is the main seal, and the other is the standby seal. Under normal conditions, one seal bears all or most of the load, while the other does not bear or bear a small part of the pressure drop. The process gas leaked through the main seal is led to the flare for combustion, and the remaining small part of the process gas is led to the safety zone for venting through the secondary seal. When the main seal fails, the secondary seal can play an auxiliary safety role.
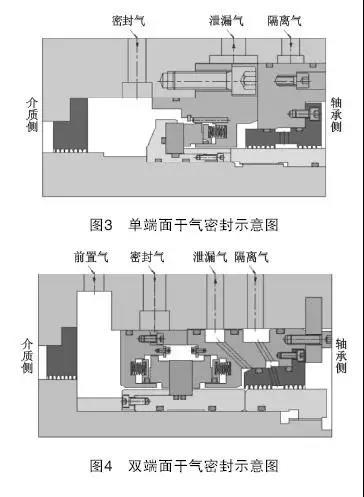
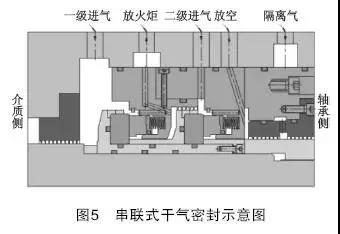
Common causes of damage
1. During the use of dry gas seal under the reverse direction of one-way groove or low-speed working condition, the installation of drive end and non drive end is reversed due to the installation error, and the reverse direction working condition and low-speed warm-up working condition are inevitable when the unit is shut down, resulting in ring breakage and seal damage. In serious cases, the ring is directly broken.
2. The rear isolation seal fails, and the outer seal is polluted. During use, the seal face may be polluted by lubricating oil due to design or operation reasons. For example, the bearing cavity is not emptied smoothly (the filter screen of the breathing cap is blocked), the gas flow rate is too small due to the low design gas flow rate, the number of labyrinth teeth or the gap is not appropriate, the orifice plate is too small, the system control problem, nitrogen fluctuation or gas supply interruption, wrong starting and stopping operation sequence, misoperation, etc.
3. The front labyrinth of the compressor failed and the seal polluted The front labyrinth seal of the compressor was severely worn, resulting in the process gas flowing back to the sealing surface of the dry seal. See Figure 6 for the polluted seal.
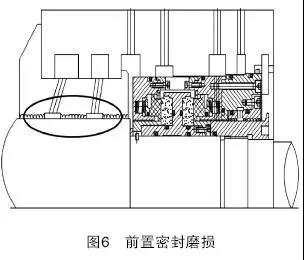
4. Improper handling of startup and shutdown, seal pollution During startup and shutdown, it is not easy to ensure the flow of a seal gas, and the gas in the machine is easy to reverse channeling, resulting in pollution of a seal end face. Therefore, the pressure may be low and the leakage may be large during the initial start-up pressurization process. Before the unit is ready for start-up and stamping, the seal gas for start-up shall be injected through the control system to avoid the pollution of seal caused by reverse channeling of process gas; In the process of shutdown, the gas source shall be switched in time to avoid reverse channeling of process gas, pollution and sealing; During shutdown, avoid sealing pollution due to operation and other reasons.
5. During normal operation, the filter system fails, and seal pollution may occur in the field operation of dry gas seal. The seal gas may carry liquid seriously, exceeding the filter processing capacity; The filter is blocked and is not switched in time, causing damage to the filter element; The air source contains a large amount of fine powder, whose particle size is smaller than the precision of the filter, which exceeds the processing capacity of the filter, but the total amount is large, which has an impact on the seal and the system, leading to the failure of the filter system, thus polluting the seal, leading to failure.
6. Seal failure caused by the unit During the normal operation of the carrier gas compressor in a chemical plant, the vibration value of the unit suddenly rose in a straight line, exceeding the measurement range of the instrument, followed by the unit seal leakage exceeding the standard. After disassembly, it was found that the seal moving ring was broken, mainly because the balance disc of the heat sleeve on the main shaft was loose, which caused axial displacement and contact wear with the stator, which led to the increase of the vibration value of the unit and exceeded the bearing range of the seal, leading to seal damage.
7. The ethylene compressor of a chemical plant was misoperated on site, and the unit had been operating normally for about 2 years. The seals at both ends suddenly failed at the same time, and the seal ring was damaged. It was found during later troubleshooting that the temperature was low in winter, and the operator opened the seal gas heater out of kindness, which caused the seal ring to burst due to sudden temperature change.
Precautions for maintenance and operation
1. Operating limit of dry gas seal The axial displacement of dry gas seal is allowed to be 2.5 mm; The radial runout is allowed to be 0.6 mm; Able to withstand short time low-speed pulse barring; Bearing API617 vibration tolerance requirements; It can bear back pressure not more than 1 MPa in static state and not in dynamic state.
2. Precautions for dry gas seal operation: clean, dry gas that is not carbonized or polymerized under certain temperature and pressure shall be used as the working gas source of dry gas seal; Always ensure that the upstream and downstream differential pressure of each seal face of dry gas seal is positive, and the one-way rotating groove cannot rotate in reverse direction.
In daily normal operation, the dry gas seal body basically does not need special operation and maintenance, but in the process of process condition fluctuation and startup and shutdown, it is necessary to pay attention to whether the flow and pressure parameters are within the normal value range given by the seal manufacturer. Especially in the process of startup and shutdown, the operation shall be strictly in accordance with the sequence provided by the seal manufacturer. Generally speaking, during startup, the isolation gas shall be put in first and then the bearing lubricating oil. When parking, vice versa.
During routine maintenance, the dry gas seal control system needs to be regularly inspected and maintained to check whether the filter is blocked, whether the insulation and heat tracing are normal, and whether the instruments and meters are normal. Generally speaking, the sealing operation performance can be basically guaranteed by ensuring that the values of all displayed instruments are within the normal range.
3. Storage of dry gas sealing spare parts Dry gas sealing spare parts are generally stored in ventilated, dark and dry rooms with room temperature not lower than - 15 ℃ and not higher than 40 ℃. Since the date of delivery, the storage time of sealing products is 3 years. Dry gas seals over 3 years should be sent back to the original manufacturer for inspection, replacement of auxiliary sealing rings and testing before use.